Imagine building a house with misshapen bricks. It would be a tedious task, with uneven gaps and a wobbly final structure. That’s exactly what working with irregular-shaped metal powders can be like in the world of Additive Manufacturing (AM), also known as 3D printing. Here’s where spheroidization powders come to the rescue, acting as the smooth, uniform building blocks for creating intricate and robust metal objects.
What is Spheroidization Powder?
Spheroidization is a process that transforms irregular, angular metal powders into near-perfect spheres. Think of a pile of pebbles getting magically rounded into marbles. This transformation brings a multitude of benefits to the AM process, making it more efficient and reliable.
Here’s a table summarizing the key aspects of spheroidization powders:
기능 | 설명 |
---|---|
프로세스 | Transformation of irregular metal powders into near-perfect spheres |
혜택 | Improved flowability, packing density, and printability |
애플리케이션 | Additive Manufacturing (3D printing) of metal parts |
Result | Stronger, more consistent, and higher-quality 3D printed objects |
But why are these spherical shapes so crucial? Let’s delve deeper.
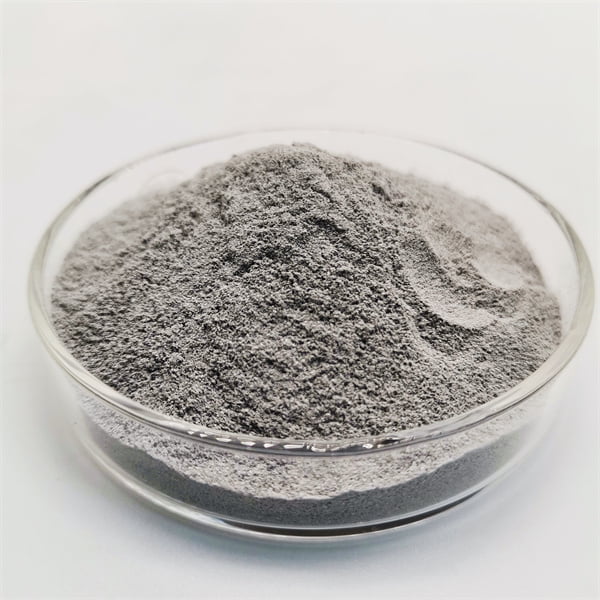
장점 Spheroidization Powders
Spheroidization powders offer a significant edge over their non-spherical counterparts. Here’s a breakdown of the key advantages:
- 향상된 흐름성: Imagine pouring sand versus ball bearings. Spherical particles flow freely due to minimal friction, just like ball bearings. This translates to smoother powder movement within the AM machine, ensuring consistent layer formation during printing.
- 향상된 포장 밀도: Imagine packing oranges versus misshapen fruits. Spheres pack together much more efficiently, maximizing the amount of powder utilized in each layer. This leads to denser and stronger final printed parts.
- 분리 감소: Non-spherical powders tend to segregate, with larger particles settling out first. This can lead to inconsistencies in the printed object. Spherical powders mix more uniformly, minimizing segregation and ensuring consistent material properties throughout the build.
- 뛰어난 표면 마감: Imagine a brick wall versus a smooth sphere. Just like a sphere, spheroidized powders create smoother surfaces on the printed object due to minimal inter-particle contact points. This reduces the need for extensive post-processing steps like grinding or polishing.
- Minimized Waste: Improved flowability and packing density lead to less powder waste during the printing process. This translates to cost savings and reduced environmental impact.
Here’s a table comparing the advantages of spheroidization powders with non-spherical powders:
기능 | Spheroidization Powders | Non-Spheroidization Powders |
---|---|---|
유동성 | 우수 | Poor |
포장 밀도 | 높음 | 낮음 |
분리 | 최소 | Significant |
표면 마감 | Smooth | Rough |
Waste | 낮음 | 높음 |
With these advantages, spheroidization powders become the preferred choice for a wide range of AM applications.
Applications of Spheroidization Powders
The world of AM is rapidly expanding, and spheroidization powders are fueling this growth across various industries:
- 항공우주: Spheroidized powders are used to create lightweight, high-strength components for aircraft, satellites, and spacecraft. Imagine printing a complex rocket engine nozzle with intricate cooling channels – all thanks to the smooth flow and consistent properties of spheroidized powders.
- 의료 기기: Custom implants, surgical tools, and prosthetics benefit from the high precision and biocompatibility offered by AM with spheroidized powders. Think of a perfectly contoured hip implant, printed with minimal surface roughness for optimal tissue compatibility.
- 자동차: From lightweight car parts to intricate heat exchangers, spheroidized powders are enabling the creation of complex and high-performance automotive components. Picture a customized gear shifter, printed with a smooth finish and strong internal structure.
- 소비재: The possibilities are endless! Imagine customized jewelry, sporting equipment, or even musical instruments – all printed with high accuracy and a beautiful finish using spheroidized powders.
These are just a few examples, and the potential applications of spheroidization powders in AM are constantly evolving.
종류 Spheroidization Powders
Now that you understand the benefits and applications, let’s explore the different types of spheroidization powders available:
Types of Spheroidization Powders :
금속 분말 모델 | 설명 |
---|---|
316L 스테인리스 스틸 | A versatile austenitic stainless steel powder known for its excellent corrosion resistance and biocompatibility. Perfect for medical implants, chemical processing equipment, and marine applications. |
티타늄 6Al-4V (Ti-6Al-4V) | A high-strength, low-weight titanium alloy widely used in aerospace, medical, and sporting goods applications. Its excellent strength-to-weight ratio makes it ideal for components requiring both lightness and durability. |
인코넬 625 | A superalloy renowned for its exceptional resistance to high temperatures, oxidation, and corrosion. This makes it perfect for jet engine components, heat exchangers, and parts exposed to harsh environments. |
Aluminum Si10Mg (AlSi10Mg) | A popular aluminum alloy known for its good castability, machinability, and weldability. Due to its combination of strength and lightweight properties, it’s widely used in automotive parts, electronic enclosures, and other applications requiring a balance of performance and weight. |
구리 | Pure copper powders offer excellent thermal and electrical conductivity, making them ideal for applications like heat sinks, electrical components, and even 3D-printed antennas. |
니켈 | Spheroidized nickel powders offer superior flowability and packing density, making them well-suited for applications requiring high purity and precise control over electrical properties. Think of intricate electrodes or microfluidic components. |
코발트 크롬(CoCr) | This biocompatible alloy is often used in medical implants, particularly for its high strength, wear resistance, and corrosion resistance. Imagine a custom-made knee implant, printed with a smooth surface and excellent long-term performance. |
공구강 | Various grades of tool steel powders are available, offering a range of hardness, wear resistance, and toughness. These are perfect for creating custom cutting tools, molds, and dies with precise geometries and superior performance. |
텅스텐 | Known for its exceptional density and high melting point, tungsten powders are used in applications requiring high strength and resistance to extreme temperatures. Imagine a custom-designed heat sink for a high-powered laser system. |
It’s important to note that this is not an exhaustive list, and new metal powder options are constantly being developed. The choice of the specific powder depends on the desired properties of the final printed object and the specific application.
사양, 크기, 등급 및 표준
When selecting spheroidization powders, several factors need to be considered:
- 파우더 크기: Particle size distribution (PSD) plays a crucial role in the printing process. Finer powders offer smoother surface finishes but may be more prone to challenges like agglomeration (clumping). Coarser powders can be easier to handle but may lead to a rougher surface finish.
- 파우더 등급: The purity and chemical composition of the powder can significantly impact the final properties of the printed object. High-grade powders are often used for critical applications requiring exceptional performance.
- 표준: Several industry standards govern the production and quality control of metal powders for AM. These standards ensure consistent performance and material properties. Common standards include ASTM International (ASTM) and the International Organization for Standardization (ISO).
Here’s a table outlining some of the typical specifications, sizes, grades, and relevant standards for spheroidization powders:
기능 | 설명 | 예 |
---|---|---|
입자 크기 분포(PSD) | Range of particle diameters within the powder | D10: 10 µm, D50: 45 µm, D90: 75 µm |
Powder Grades | Purity level and additional elements | 316L Stainless Steel (UNS S31603) |
표준 | Industry regulations for quality control | ASTM B294 |
Understanding these specifications allows for the selection of the most suitable spheroidization powder for a specific application.
We’ll continue our exploration of spheroidization powders in the next section, discussing the pros and cons, addressing frequently asked questions, and providing some resources for further exploration.
장점과 단점 Spheroidization Powders
Spheroidization powders offer a significant advantage in the realm of Additive Manufacturing. However, like any technology, they come with their own set of considerations.
Pros of Spheroidization Powders:
- Enhanced Printability: The spherical shape translates to smoother powder flow, improved packing density, and minimized segregation. This leads to a more consistent and reliable printing process, reducing the risk of printing defects and ensuring high-quality final parts.
- 우수한 머티리얼 속성: Denser packing and minimized internal voids in the printed object contribute to improved mechanical strength, fatigue resistance, and overall performance. Imagine a lighter-weight aircraft component with exceptional strength thanks to the use of spheroidized powders.
- 낭비 감소: Efficient powder flow and packing density minimize wasted material during the printing process. This translates to cost savings and a more environmentally friendly approach to AM.
- 표면 마감 개선: The spherical nature of the powder leads to smoother surfaces on the printed object, reducing the need for extensive post-processing steps like grinding or polishing. Think of a medical implant with a smooth surface finish for optimal biocompatibility.
- Wider Range of Materials: Spheroidization techniques can be applied to a variety of metals, expanding the possibilities for AM applications. This allows for the creation of components with diverse properties and functionalities.
Cons of Spheroidization Powders
- 비용: The spheroidization process itself can add to the overall cost of the metal powder. However, the benefits in terms of printability, material properties, and reduced waste often outweigh the initial cost increase.
- 파우더 특성: Not all spheroidized powders are created equal. Factors like surface morphology and flowability characteristics can vary depending on the specific material and spheroidization technique used. Careful selection of the powder is crucial for optimal printing results.
- Applicability: While spheroidization offers significant advantages, it might not be necessary for all AM applications. For simpler geometries or less critical parts, non-spherical powders might be sufficient.
Here’s a table summarizing the pros and cons of spheroidization powders:
기능 | 장점 | 단점 |
---|---|---|
인쇄 가능성 | Enhanced | |
머티리얼 속성 | 우수 | |
Waste | Reduced | |
표면 마감 | Improved | |
Material Range | 더 넓게 | |
비용 | Higher (potentially) | |
파우더 특성 | Can vary | |
Applicability | Not universally necessary |
By understanding both the advantages and limitations of spheroidization powders, users can make informed decisions about their suitability for specific AM projects.
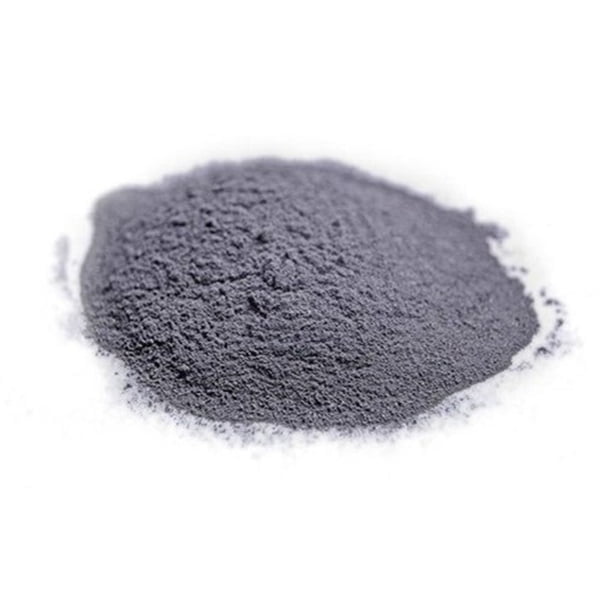
자주 묻는 질문
Q: Are spheroidization powders always necessary for AM?
A: Not necessarily. For simpler geometries or less critical parts, non-spherical powders might be sufficient. However, for high-performance applications requiring intricate details, consistent material properties, and a smooth surface finish, spheroidization powders offer significant advantages.
Q: What are some of the common spheroidization techniques?
A: Several techniques exist, including plasma atomization, gas atomization, and rotary atomization. Each technique has its own strengths and weaknesses, and the choice depends on the specific metal powder being processed.
Q: Where can I find more information about spheroidization powders and their suppliers?
A: Several resources are available online and through industry publications. Reputable metal powder suppliers often provide detailed information about their spheroidization processes and the powders they offer. Manufacturing associations and research institutions can also be valuable sources of information.
Here’s a table presenting the FAQs in a clear format:
질문 | 답변 |
---|---|
Are spheroidization powders always necessary for AM? | Not always, but they offer significant advantages for high-performance applications. |
What are some common spheroidization techniques? | Plasma atomization, gas atomization, rotary atomization (each with specific strengths and weaknesses). |
Where can I find more information? | Online resources, industry publications, metal powder suppliers, manufacturing associations, and research institutions. |
결론
Spheroidization powders are revolutionizing the world of Additive Manufacturing. By transforming irregular metal powders into near-perfect spheres, they pave the way for smoother printing processes, stronger and more consistent final parts, and a wider range of AM applications. While there are some cost considerations and variations in powder characteristics, the overall benefits make spheroidization powders a powerful tool for the future of AM.