Imagine building intricate objects, not with bricks and mortar, but with layers of pure metal! That’s the power of 3D printing, and 구형 금속 분말 is the secret ingredient that makes it all possible. But how exactly do these tiny, perfect spheres transform into awe-inspiring metal creations? Buckle up, because we’re diving deep into the fascinating world of spherical 3D printed metal powder preparation!
The Power of the Sphere: Why Spherical Matters
Spherical metal powder might seem like a minor detail, but it has a massive impact on the success of 3D printing. Here’s why:
- 흐름성: Imagine pouring sand through an hourglass. Spheres flow freely, just like metal powder needs to in the 3D printer. Irregular shapes can get caught, disrupting the printing process and potentially damaging the machine.
- 포장 밀도: Think of packing oranges in a box. Spheres pack together much more efficiently than oddly shaped particles. This translates to denser printed objects, which are generally stronger and more durable.
- Melting Consistency: During printing, the metal powder gets blasted by a laser or electron beam, melting it layer by layer. Spheres offer a more uniform surface area for the energy to interact with, leading to more consistent melting and better quality prints.
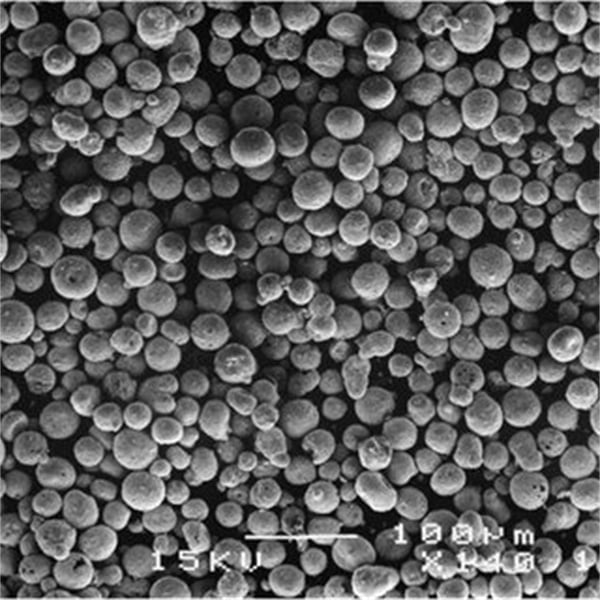
So, how do we turn molten metal into these magical spheres? Let’s explore the three main methods:
1. The Aerosol Method: A Classic Workhorse
The aerosol method, also known as gas atomization, has been around for decades and is still a popular choice. Here’s how it works:
- Molten Metal Magic: The metal is first heated to its molten state in a furnace. Think of a pot of glowing liquid metal!
- 분석하기: This molten metal is then forced through a tiny nozzle at high pressure. Imagine squeezing toothpaste through a narrow opening.
- The Power of Gas: A high-velocity gas stream breaks the molten metal stream into tiny droplets. Picture a garden hose spraying water, but with molten metal instead!
- 응고 심포니: These droplets rapidly cool and solidify in mid-air due to their small size, forming near-perfect spheres thanks to surface tension (the same force that makes water droplets round).
- Sifting and Sorting: Finally, the metal powder is collected, classified according to size, and any impurities are removed.
The aerosol method is a mature and reliable process, but it has limitations. It can be less efficient for some metals and might struggle to achieve perfectly spherical particles for very fine powders.
2. Plasma Atomization Method: Superheating for Superior Spheres
For a more high-tech approach, we turn to plasma atomization. This method cranks things up a notch with the power of plasma:
- Plasma Powerhouse: A plasma torch generates an incredibly hot ionized gas that melts the metal feedstock. Think of a super-powered blowtorch that uses electricity to create intense heat.
- Centrifugal Force Fun: The molten metal is then fed into a rapidly spinning atomizer. Imagine a spinning bowl filled with molten metal!
- Breaking Up is Hard to Do (But Worth It): The centrifugal force throws the molten metal outwards, breaking it into fine droplets. Picture mud flying off a tire as it spins!
- Cooling Down: Similar to the aerosol method, these droplets rapidly cool and solidify mid-air, forming near-perfect spheres.
Plasma atomization offers several advantages. It can handle a wider range of metals, including those with high melting points, and produces more uniform and spherical powders compared to the aerosol method. However, it’s also a more complex and expensive process.
3. Spheroidization Method: Reshaping the Irregular
Sometimes, the initial metal powder might not be perfectly spherical. That’s where the spheroidization method comes in. Here’s how it refines the powder:
- Heating Up for Change: The metal powder is fed into a heated chamber.
- Sticky Situation: A binder or molten metal is introduced, causing the particles to partially melt and stick together. Imagine adding glue to a pile of sand!
- Shaping Up: The mixture is then subjected to mechanical forces like tumbling or shearing. Picture a giant rolling pin smoothing out the sand-glue mixture!
- Breaking Apart: Finally, the cooled-down particles are separated, resulting in a more spherical powder.
The spheroidization method is a good option for refining existing powder or for materials that are difficult to atomize using other methods. However, it can add an extra step to the process and might affect the particle size distribution.
Choosing the Right Method: A Balancing Act
The best method for preparing 구형 금속 분말 depends on several factors, including:
- The Metal: Different metals have varying melting points, flow characteristics, and reactivity. Some methods, like plasma atomization, are better suited for high-melting-point metals like titanium or tantalum.
- Desired Powder Properties: The size, distribution, and sphericity of the powder all play a role in the final 3D printed product. The chosen method should be able to achieve the desired powder characteristics.
- Cost and Efficiency: The aerosol method is generally the most cost-effective, but plasma atomization might be necessary for specific metals or applications. Spheroidization adds an extra processing step, impacting cost and production time.
Here’s an analogy to understand the trade-offs: imagine baking a cake. You can use a simple box mix (aerosol method) for a quick and easy bake, but it might not be as customizable. For a gourmet cake (high-performance metal), you might need a more complex recipe with specific ingredients (plasma atomization), but the result will be superior. Finally, adding frosting and decorations (spheroidization) can enhance the final product, but it takes additional time and effort.
Emerging Techniques and Future Trends
The world of spherical metal powder preparation is constantly evolving. Here’s a glimpse into some exciting advancements:
- Rotary Electrode Process (REP): This method utilizes a rapidly spinning molten metal feedstock that breaks into droplets due to centrifugal force. It offers high efficiency and can produce fine spherical powders.
- Electrode Induction Melting (EIM): This technique uses an induction coil to melt the metal feedstock, which is then atomized with a high-pressure gas stream. It’s particularly well-suited for reactive metals like aluminum.
- Nanoparticle Production: Researchers are exploring methods for producing even finer spherical metal powders in the nanometer range. These powders could enable the creation of high-strength, lightweight materials with unique properties.
의 영향 Spherical Metal Powders
The development of spherical metal powders has revolutionized the field of 3D printing. It has opened doors to a vast array of applications, including:
- 항공우주: Lighter, stronger components for airplanes and rockets can be manufactured using 3D printing with spherical metal powders.
- 의료용 임플란트: Customized prosthetic limbs and other implants can be created with biocompatible metal powders.
- 자동차: Complex and lightweight parts can be produced for vehicles, leading to improved fuel efficiency and performance.
- 소비재: From customized jewelry to intricate gadgets, the possibilities for creating unique metal objects are endless.
As the technology continues to develop, we can expect even more innovative applications for spherical metal powders, pushing the boundaries of what’s possible in manufacturing.
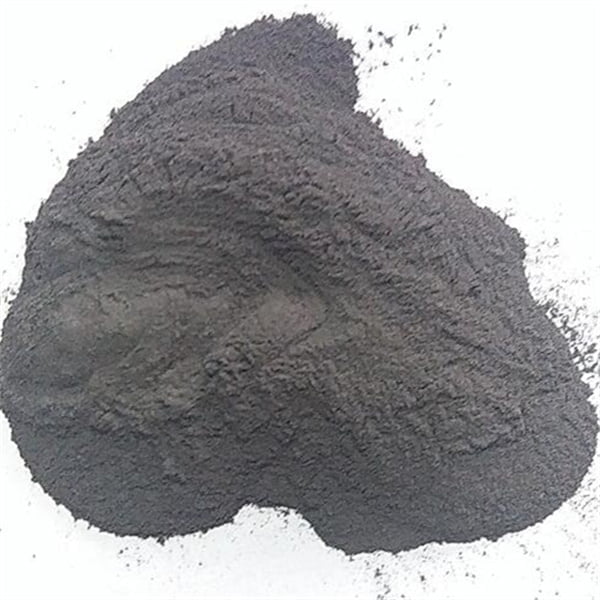
자주 묻는 질문
Table 1: Frequently Asked Questions about Spherical Metal Powders
질문 | 답변 |
---|---|
3D 프린팅에 구형 금속 분말을 사용하면 어떤 이점이 있나요? | Spherical metal powders offer improved flowability, packing density, and melting consistency, leading to better quality and efficiency in the 3D printing process. |
What are the different methods for producing spherical metal powders? | The three main methods are aerosol (gas) atomization, plasma atomization, and spheroidization. |
Which method is the best for producing spherical metal powders? | The best method depends on the specific metal, desired powder properties, and cost considerations. |
What are some emerging techniques for producing spherical metal powders? | Techniques like Rotary Electrode Process (REP) and Electrode Induction Melting (EIM) are gaining traction for specific applications. |
What are some of the applications of spherical metal powders? | Spherical metal powders are used in various industries, including aerospace, medical implants, automotive, and consumer goods. |
결론
The journey from raw metal to perfectly spherical powder might seem complex, but it’s a crucial step in the magic of 3D printing. By understanding the different methods and their advantages, we can appreciate the innovation behind this technology and its potential to revolutionize how we create objects in the future. As these techniques continue to evolve, the possibilities for creating complex, high-performance metal parts using 3D printing are truly limitless.