내화 분말 내화 재료는 까다로운 산업 분야에서 사용되는 매우 높은 내열성을 지닌 특수한 무기 비금속 재료입니다. 이 종합 가이드는 기술 전문가와 구매자가 일반적인 구성, 중요 특성 데이터, 제조 공정, 응용 분야, 사양 및 공급업체를 아우르는 내화 분말의 모든 주요 특성을 이해할 수 있도록 돕습니다.
내화 분말 재료 개요
내화 분말은 1000°C 이상의 고온에서 강도와 형태를 유지하며 뛰어난 열 안정성을 보여주는 미세하게 분할된 불활성 비금속 재료로 구성됩니다. 주요 하위 클래스에는 산화물, 탄화물, 질화물 및 세라믹이 포함됩니다.
크리티컬 속성:
- 1000°C 이상의 내열성
- 열 충격에 대한 내성
- 부식에 대한 내구성
- 높은 융점
- 구조적 무결성 유지
뛰어난 성능으로 용광로, 보일러, 가마, 원자로 및 기존 소재가 빠르게 고장 나는 기타 극한의 열 환경에서 성능을 강화합니다.
일반적인 구성
재질 | 역할 | Wt% 범위 |
---|---|---|
알루미나 | 열 속성 | 40-100% |
실리카 | 행렬 바인딩 | 0-60% |
마그네시아 | 성능 저하 방지 | 0-20% |
흑연 | 열 충격 저항력 향상 | 0-15% |
주요 구성 요소의 균형을 맞추면 열용량, 단열, 내식성, 융점, 비용 등의 특성을 최적화할 수 있습니다.
내화 분말의 주요 유형
유형 | 설명 |
---|---|
융합 | 1800°C 이상을 견디는 극도의 순도 |
소결 | 파우더 프레스/소성, 비용 절감 |
실리콘 카바이드 | 열전도율이 높은 세라믹 |
크로마이트 | 슬래그, 금속 침투에 대한 내성 |
지르코니아 | 열 충격 저항 |
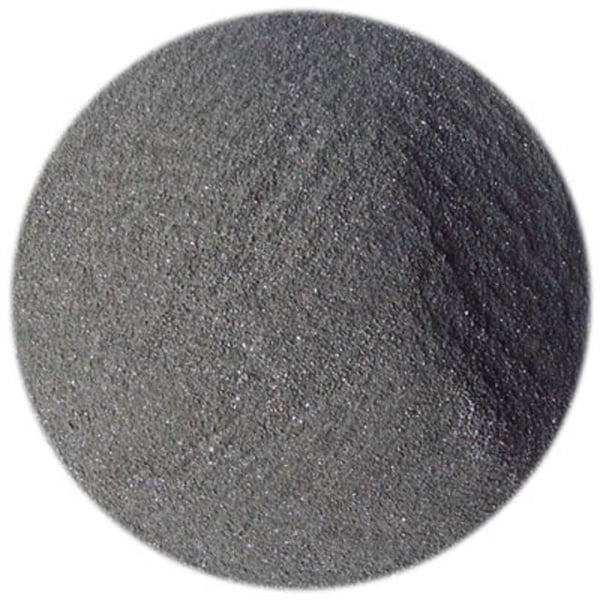
내화 분말 재료 제조 공정
혜택 | 설명 | 영향 |
---|---|---|
고밀도, 그물 모양에 가까운 부품 | EBM은 사용되는 금속 분말의 이론적 밀도 99.5%를 초과하는 밀도의 부품을 제작합니다. 따라서 다른 적층 제조 방식에서 흔히 발생하는 다공성(작은 공기 주머니)을 제거하여 강도, 내피로성, 치수 정확도가 뛰어난 부품을 제작할 수 있습니다. | 이를 통해 항공우주(터빈 블레이드, 엔진 하우징), 의료(치과 임플란트, 보철), 자동차(경량, 고성능 부품) 산업의 까다로운 응용 분야를 위한 기능성 금속 부품을 제작할 수 있습니다. |
우수한 기계적 특성 | EBM의 고진공 환경과 정밀한 용융 공정은 산화와 오염을 최소화하여 금속 분말의 고유한 특성을 보존합니다. 그 결과 인장 강도, 크리프 저항(고온에서 응력 하에서 변형을 견디는 능력), 파단 인성이 뛰어난 부품이 탄생합니다. | EBM으로 생산된 부품은 상당한 하중을 견디고 고온에서도 효과적으로 작동하며 균열 전파를 방지할 수 있어 열악한 환경에서 내구성과 구조적 무결성이 요구되는 애플리케이션에 이상적입니다. |
내화성 및 반응성 금속 처리 | 높은 융점과 반응성으로 인해 제한을 받는 기존 제조 방식과 달리 EBM은 티타늄 합금, 탄탈륨, 인코넬과 같은 까다로운 소재를 가공하는 데 탁월합니다. 진공 환경은 산화를 방지하고 용융 공정을 정밀하게 제어할 수 있어 성공적인 제작을 보장합니다. | 이를 통해 부품의 중량 대비 강도, 생체 적합성(생체 조직과의 호환성), 고온 성능이 요구되는 항공우주 및 바이오메디컬과 같은 산업에서 설계 가능성을 넓힐 수 있습니다. |
복잡한 형상을 위한 자유로운 설계 | EBM의 레이어별 접근 방식은 기존 기술로는 불가능한 복잡한 내부 피처, 채널, 격자 구조를 만들 수 있습니다. 이러한 설계 유연성은 무게 배분을 최적화하고 열 전달을 개선하며 뛰어난 기능을 갖춘 부품을 제작할 수 있게 해줍니다. | 이러한 이점은 엔진 효율을 위해 복잡한 냉각 채널을 갖춘 경량 고강도 부품이 중요한 항공우주와 같은 산업에서 제품 설계를 혁신적으로 개선할 수 있습니다. 또한 환자의 해부학적 구조와 완벽하게 일치하는 맞춤형 의료용 임플란트를 제작할 수 있습니다. |
최소한의 지원 구조 | EBM으로 생산된 부품의 고유 강도가 높기 때문에 제작 과정에서 최소한의 서포트 구조만 필요합니다. 따라서 후처리 시간과 재료 낭비가 줄어들 뿐만 아니라 최종 부품의 서포트 구조가 손상될 위험도 줄어듭니다. | 따라서 제작 시간이 단축되고 전체 비용이 절감되며 기존 방식으로는 지원하기 어렵거나 불가능한 복잡한 형상을 제작할 수 있습니다. |
재료 낭비 감소 | EBM은 적층 제조 공정으로, 원하는 모양을 만들기 위해 재료를 한 층씩 추가하는 방식입니다. 이는 최종 형태를 얻기 위해 원재료의 상당 부분을 제거하는 기계 가공과 같은 감산 기술에 비해 재료 낭비를 최소화합니다. | 이러한 이점은 재료 활용도를 극대화하여 지속 가능성을 높이고 생산 비용을 절감합니다. 또한 빌드 챔버에서 사용하지 않은 파우더를 다음 빌드에 재사용할 수 있어 낭비를 더욱 최소화할 수 있습니다. |
내화 분말 재료의 특성
속성 | 일반 값 |
---|---|
융점 | 1600°C 이상 |
밀도 | 2 - 6g/cm3 |
압축 강도 | 20 - 100 MPa |
굴곡 강도 | 10 - 60 MPa |
골절 인성 | 2 - 10 MPa-m^1/2 |
열 전도성 | 20 - 100 W/m-K |
전기 저항 | 10^8 - 10^13 옴-cm |
최대 서비스 온도 | 1200°C - 2000°C |
녹는점, 열용량, 열충격 저항, 절연 값, 화학적 관성 및 비용과 같은 요구 사항의 균형을 고려하여 선택이 결정됩니다.
내화 분말 재료의 응용
산업 | 애플리케이션 | 재질 | 활용되는 속성 |
---|---|---|---|
항공우주 | * Turbine Blades * Rocket Nozzles * Heat Shields |
* Tungsten * Tantalum * Rhenium |
* High Melting Points (>3000°C) * Excellent Mechanical Strength at High Temperatures * Superior Oxidation Resistance |
자동차 | * Spark Plug Electrodes * Exhaust Valves * Turbocharger Components |
* Tungsten * Molybdenum * Nickel Alloys |
* High Electrical Conductivity * Wear Resistance * Thermal Shock Resistance |
전자 제품 | * High-Temperature Resistors * Capacitors * Electrical Contacts |
* Tungsten * Molybdenum * Silver |
* High Melting Points * Low Resistivity * Arc Erosion Resistance |
에너지 | * Linings for Furnaces in Power Plants * Molten Salt Reactors |
* Silicon Carbide * Alumina * Zirconia |
* Excellent Thermal Conductivity * High Chemical Stability * Resistance to Molten Salts |
의료 | * Hip and Knee Replacements * Dental Implants * Radiation Shielding |
* Titanium Alloys * Tantalum * Tungsten |
* Biocompatibility * High Strength-to-Weight Ratio * X-Ray Opacity |
화학 처리 | * Reactors for Harsh Chemical Environments * High-Temperature Piping * Heat Exchangers |
* Tantalum * Zirconium * Nickel Alloys |
* Corrosion Resistance * High Strength at Elevated Temperatures * Excellent Formability |
툴링 | * Cutting Tools for High-Strength Materials * Dies for Metal Forming * Molds for Glass and Ceramics |
* Tungsten Carbide * Boron Nitride * Diamond Powders |
* Exceptional Hardness * High Wear Resistance * Low Thermal Expansion |
적층 제조 | * 3D Printing of Complex Metal Components * Repair of Worn or Damaged Parts |
* Inconel Powders * Cobalt Chrome Alloys * Titanium Powders |
* High Powder Flowability for Precise Printing * Excellent Sintering Properties * Tailored Microstructures for Specific Applications |
사양 및 등급
속성 | 설명 | 선택 시 주요 고려 사항 |
---|---|---|
화학 성분 | The primary building blocks of the powder, typically metal oxides, carbides, nitrides, or ceramics. | * Dominant Oxide: Alumina (Al2O3) offers excellent high-temperature strength but lower thermal shock resistance. Silica (SiO2) provides good chemical resistance but lower refractoriness. Magnesia (MgO) excels in resisting slag attack but hydrates readily. * Secondary Additives: Calcia (CaO) enhances slag resistance, while chromia (Cr2O3) improves wear resistance. * 순도: Higher purity generally translates to better performance but may come at a cost increase. |
입자 크기 분포 | The range and spread of individual particle sizes within the powder. | * Average Particle Size: Finer powders offer superior packing density and surface area for bonding, but can be more susceptible to agglomeration (clumping) and hinder flow characteristics. * 입자 크기 분포: A narrow distribution ensures consistent packing and minimizes segregation during processing. Broader distributions can be beneficial for filling voids and improving packing efficiency. * Specific Applications: Processes like 3D printing often require tighter size control for optimal flow and printability. |
입자 형태학 | The shape and form of individual particles. | * Shape: Spherical particles typically pack more efficiently, while angular particles can create a mechanical interlocking effect for improved strength. * 표면적: Higher surface area powders offer better bonding potential but can also increase reactivity. * Morphology Control: Certain applications may prioritize specific shapes, such as platelets for enhanced thermal conductivity. |
겉보기 밀도 | The mass of powder per unit volume in its loose, uncompacted state. | * Packing Efficiency: Higher apparent density indicates better packing efficiency and can reduce material usage. * 흐름성: Powders with lower apparent density typically exhibit better flow characteristics for easier handling and processing. * 녹색 강도: Apparent density can influence the green strength (pre-fired) of shaped components. |
벌크 밀도 | The mass of powder per unit volume after undergoing a standardized tapping or vibration procedure. | * Compaction Efficiency: Bulk density reflects how well the powder can be compacted, impacting final product density and properties. * 다공성: Lower bulk density indicates higher porosity, which can influence thermal insulation properties but may decrease mechanical strength. * Material Handling: Bulk density affects how much powder can be efficiently stored or transported in a given volume. |
비중 | The ratio of a material’s density to the density of water. | * Refractory Selection: High specific gravity materials generally offer superior heat resistance but may come with increased weight considerations. * 비용 효율성: Lighter materials with lower specific gravity can be more cost-effective to transport and handle. |
Refractoriness | The maximum temperature a material can withstand without melting or losing its structural integrity. | * 신청 요건: The refractory powder needs to exceed the expected operating temperature in the final application. * Chemical Environment: Certain atmospheres can affect refractoriness. For example, reducing environments can degrade some oxides. |
열 전도성 | The material’s ability to conduct heat. | * Heat Transfer Management: High thermal conductivity can be beneficial for applications requiring efficient heat transfer, such as heat exchangers. * Thermal Insulation: Low thermal conductivity is desirable for applications needing to retain heat, such as furnace linings. |
열 팽창 | The amount a material expands upon heating. | * Thermal Shock Resistance: Materials with lower thermal expansion are generally more resistant to cracking and spalling due to rapid temperature changes. * 차원 안정성: Matching the thermal expansion coefficient of the refractory powder to the substrate material minimizes stress development during thermal cycling. |
내화학성 | The material’s ability to withstand attack from corrosive chemicals and molten metals/slags. | * Specific Aggressive Agents: Selection should consider the types of chemicals the refractory will encounter in the application. * Acidity/Alkalinity: Acidic or basic environments can degrade specific refractory materials. |
Other Performance Characteristics | Additional properties depending on the specific application, such as erosion resistance, electrical conductivity, or wear resistance. | * Focus on Needs: Identify the critical performance factors for the intended use case and choose a powder that excels in those areas. * Trade-offs: Often, there will be trade-offs between various properties. Selecting the optimal material involves prioritizing the most relevant characteristics. |
내화 분말 자재 공급업체
회사 | 위치 |
---|---|
생고뱅 | 글로벌 |
RHI 마그네시타 | 브라질, 오스트리아, 중국 |
크로사키 하리마 | 일본 |
베수비오 | 유럽, 미국 |
모건 어드밴스드 머티리얼즈 | 영국, 미국 |
가격 견적
등급 | kg당 가격 |
---|---|
표 형식 알루미나 | $10-30 |
실리콘 카바이드 | $50-150 |
지르코니아 | $100-500 |
기타 | $20-100 |
규모의 경제는 비용에 영향을 미치며, 맞춤형 구성과 엄격한 품질 요건은 프리미엄을 요구합니다.
장점과 단점
장점 | 단점 |
---|---|
Unmatched Heat Resistance: Refractory powders boast exceptional thermal stability, enduring temperatures exceeding 1500°C (2732°F) without melting or degrading. This makes them ideal for lining furnaces, kilns, reactors, and other high-heat applications where traditional materials would quickly succumb. | Brittleness and Spalling: Due to their rigid structure, refractory powders can be susceptible to cracking and chipping, especially under rapid temperature fluctuations (thermal shock). This spalling can compromise the integrity of the lining, requiring repairs or replacement. |
맞춤형 성능: By carefully selecting and blending different refractory powder types (e.g., alumina, zirconia, magnesia), engineers can create customized material formulations with specific properties. This allows for optimization of factors like heat resistance, chemical compatibility, and wear resistance to precisely match the demands of the application. | Complex Installation: Unlike pre-formed bricks or shapes, refractory powders necessitate a more involved installation process. This often involves techniques like casting, gunning, or vibro-casting, requiring specialized equipment and skilled labor to achieve a dense, uniform lining. |
Versatility in Form and Function: Refractory powders offer superior design flexibility compared to pre-fabricated components. Their ability to be molded into intricate shapes enables the creation of complex furnace linings, crucibles, and other bespoke refractory elements. | 비용 고려 사항: The raw materials and processing techniques involved in producing high-performance refractory powders can translate to a higher initial cost compared to some conventional refractory materials. |
Lightweight Advantage: Refractory powders contribute to a significant weight reduction compared to traditional brick linings. This is particularly beneficial in applications where lighter weight translates to improved energy efficiency, reduced structural load, and easier handling during installation. | Potential Health Risks: Certain refractory powder compositions, particularly those containing silica or chromite, may pose health risks if inhaled. Implementing proper safety protocols and using appropriate personal protective equipment (PPE) is crucial during handling and installation. |
Enhanced Refractory Properties: By incorporating specific additives or utilizing advanced manufacturing techniques, refractory powders can be engineered to exhibit superior properties beyond basic heat resistance. This can include improved thermal shock resistance, enhanced chemical resistance to molten metals or slags, and even self-healing capabilities for extended service life. | 환경 영향: Depending on the specific composition and production methods, some refractory powders may have environmental concerns associated with their mining, processing, or disposal. Selecting eco-friendly raw materials and responsible recycling practices are important factors to consider. |
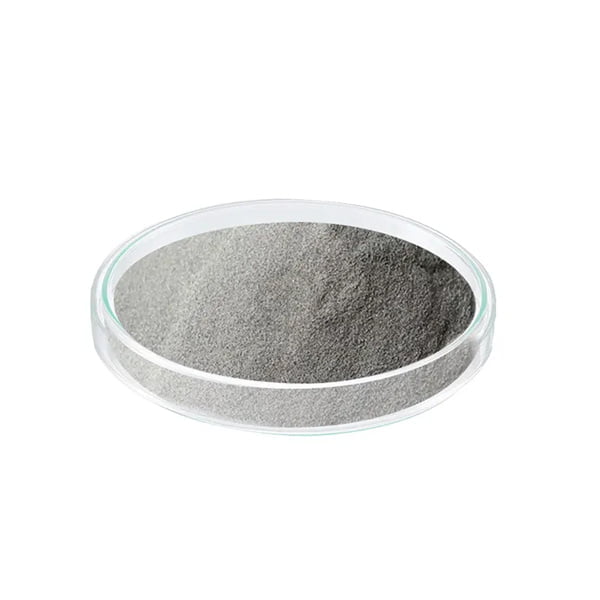
자주 묻는 질문
Q: 내화 분말과 내화 벽돌의 차이점은 무엇인가요?
A: 브릭은 사전 성형된 통합 구조물이며, 파우더는 프레스/소성 또는 첨단 적층 제조 방법을 통해 특수 내화 부품을 제작할 수 있는 원료 공급원입니다.
Q: 모든 내화성 분말을 AM 기술을 사용하여 3D 프린팅할 수 있나요?
A: 예 - 바인더 분사 및 직접 에너지 증착 인쇄는 이전에는 불가능했던 내화성 기하학적 구조에 대해 대부분의 내열성 알루미나, 지르코니아 및 탄화규소 등급과 호환되는 것으로 입증되었습니다.
Q: 어떤 내화 파우더가 가장 높은 서비스 온도를 제공하나요?
A: 초고순도 용융 뮬라이트 및 지르코니아 등급은 대체재가 녹거나 분해되는 가장 까다로운 용광로, 항공우주 및 원자력 응용 분야에서 2000°C 이상을 안정적으로 견딜 수 있습니다.
Q: 합성 내화물과 천연 내화물의 차이점은 무엇인가요?
A: 보크사이트, 마그네사이트, 점토와 같은 천연 원료를 정밀하게 제어된 파우더로 광범위하게 가공해야 합성 엔지니어링 포뮬러에서 가능한 향상된 균일성과 극한의 내열성을 달성할 수 있습니다.
결론
이 가이드는 뛰어난 내열성을 통해 가장 뜨겁고 혹독한 산업 환경에서 일반 금속 및 합금의 한계를 극복하는 특수 소재인 내화 분말에 대한 총체적인 참고 자료를 제공하는 것을 목표로 제작되었습니다. 업계 전문가와 상담하여 귀사의 특정 극한 가공 요구 사항에 맞는 고급 내화 등급을 맞춤화하는 방법에 대해 논의해 보세요. 가능성은 무궁무진합니다.