인코넬 625는 니켈-크롬-몰리브덴 합금으로 고강도, 뛰어난 내식성, 우수한 가공성으로 잘 알려져 있습니다. 열, 압력, 부식성 환경과 같은 극한의 조건에서 탁월한 성능을 요구하는 애플리케이션에 널리 사용됩니다.
인코넬 625 분말 은 이 초합금의 분말 야금 형태로, 적층 제조 및 기타 분말 기반 제조 기술에 적합한 미세한 인코넬 625 입자로 구성되어 있습니다. 이 문서에서는 인코넬 625 분말의 구성, 특성, 용도, 사양, 가격, 공급업체, 다른 합금과 비교한 장단점 등을 포함하여 인코넬 625 분말에 대한 포괄적인 개요를 제공합니다.
인코넬 625 분말의 구성
인코넬 625 합금은 니켈, 크롬, 몰리브덴, 니오븀 및 기타 합금 원소의 화학적 조성에서 유리한 특성을 얻습니다. 다음은 인코넬 625 분말의 일반적인 구성입니다:
요소 | 무게 % |
---|---|
니켈(Ni) | 58.0분 |
크롬(Cr) | 20.0-23.0 |
몰리브덴(Mo) | 8.0-10.0 |
니오븀(Nb) + 탄탈륨(Ta) | 3.15-4.15 |
철(Fe) | 최대 5.0 |
구리(Cu) | 최대 0.5 |
망간(Mn) | 최대 0.5 |
실리콘(Si) | 최대 0.5 |
알루미늄(Al) | 최대 0.4 |
탄소(C) | 최대 0.1 |
유황(S) | 최대 0.015 |
인(P) | 최대 0.015 |
붕소(B) | 최대 0.006 |
니켈과 크롬 함량이 높은 인코넬 625는 산화 및 내식성이 뛰어납니다. 몰리브덴은 내식성을 더욱 향상시킵니다. 니오브는 침전 경화를 통해 니켈 기반 매트릭스를 강화하는 데 도움을 줍니다. 철, 구리 및 기타 원소는 입자 구조를 개선하고 작업성에 기여합니다. 탄소 함량이 낮아 용접 또는 열처리 시 카바이드 침전을 최소화합니다.
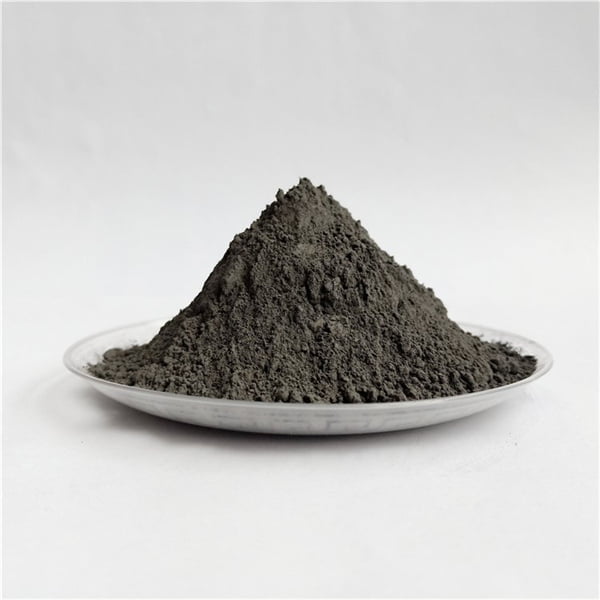
인코넬 625 분말의 특성
속성 | 설명 | 단위 | 기능에 미치는 영향 |
---|---|---|---|
화학 성분 | Inconel 625 powder is primarily composed of nickel (Ni), typically around 60-70%, with significant additions of chromium (Cr) for oxidation resistance (19-23%) and molybdenum (Mo) for high-temperature strength (8-10%). Smaller amounts of niobium (Nb), iron (Fe), and manganese (Mn) further enhance its properties. | 무게 % | The specific balance of elements determines the exceptional properties of Inconel 625, making it suitable for demanding applications. |
입자 형태학 | Inconel 625 powder is typically spherical in shape with a smooth surface. Particle size distribution is tightly controlled to ensure optimal flow characteristics for additive manufacturing processes and minimize porosity in finished parts. | Micrometers (µm) | Spherical morphology allows for even packing during printing, leading to denser parts with improved mechanical properties. Precise size distribution ensures consistent flow during the printing process. |
겉보기 밀도 | The apparent density of Inconel 625 powder refers to the mass of powder per unit volume in its loose, uncompacted state. It typically ranges from 4.5 to 5.0 g/cm³. | Grams per cubic centimeter (g/cm³) | Apparent density influences powder handling and storage requirements. It also affects the packing efficiency during printing, impacting material usage and final part density. |
탭 밀도 | Tap density represents the density of Inconel 625 powder after a standardized tapping procedure. It is generally higher than the apparent density due to the rearrangement of particles and is closer to the packing density achieved during printing. | Grams per cubic centimeter (g/cm³) | Tap density provides a more realistic picture of how efficiently the powder packs under pressure, influencing the final density and mechanical properties of printed parts. |
유동성 | Flowability refers to the ease with which Inconel 625 powder flows under gravity. It is crucial for smooth operation in additive manufacturing processes. Good flowability ensures consistent powder feeding and minimizes the risk of layer irregularities. | Seconds per 50 grams (s/50g) | Measured using standardized tests, flowability indicates how readily the powder moves, impacting powder bed formation and printability. |
Mechanical Properties (Room Temperature) | Inconel 625 powder exhibits excellent mechanical properties at room temperature. These include high tensile strength (typically exceeding 800 MPa), good yield strength (around 450 MPa), and reasonable ductility (elongation exceeding 50%). | Megapascals (MPa) and Percent (%) | The combination of high strength, good ductility, and toughness makes Inconel 625 powder suitable for applications requiring structural integrity under moderate loads. |
Mechanical Properties (Elevated Temperature) | Inconel 625 powder retains its impressive mechanical properties at elevated temperatures, a key characteristic for its use in hot sections of jet engines and other high-temperature applications. Tensile and yield strengths remain significant even at temperatures exceeding 800°C. | Megapascals (MPa) at specific temperatures (°C) | Exceptional high-temperature strength allows components made from Inconel 625 powder to function reliably under extreme thermal conditions. |
산화 저항 | Inconel 625 powder possesses outstanding resistance to oxidation due to the formation of a protective chromium oxide layer on its surface at high temperatures. This layer hinders further oxygen diffusion and prevents significant material degradation. | The excellent oxidation resistance enables Inconel 625 powder to withstand prolonged exposure to hot, oxygen-rich environments, making it ideal for applications like combustor liners and turbine blades. | |
내식성 | Inconel 625 powder demonstrates superior resistance to various corrosive environments, including aqueous solutions, acids, and alkalis. This property is attributed to the synergistic effect of chromium, molybdenum, and nickel in its composition. | The exceptional corrosion resistance allows components made from Inconel 625 powder to function reliably in harsh chemical environments, such as those encountered in chemical processing equipment and marine applications. |
응용 인코넬 625 분말
산업 | 애플리케이션 | 활용된 주요 속성 |
---|---|---|
항공우주 | * Aircraft ducting systems * Engine exhaust systems * Thrust reverser systems * Turbine shroud rings * 애프터버너 구성 요소 |
* High-temperature strength: Inconel 625 powder retains its structural integrity even under the intense heat of jet engines, enabling efficient and reliable performance. * Excellent oxidation resistance: The alloy composition minimizes the formation of oxides at elevated temperatures, preventing component degradation and ensuring smooth airflow. * Superior creep resistance: At high temperatures and constant stress, Inconel 625 powder exhibits minimal deformation, crucial for maintaining precise tolerances in critical engine parts. |
석유 및 가스 추출 | * Downhole well components * High-pressure pipelines * Processing equipment for corrosive fluids |
* Exceptional corrosion resistance: Inconel 625 powder effectively resists attack from harsh chemicals like sour gas (containing hydrogen sulfide) and chloride-rich brines, extending component lifespan in aggressive downhole environments. * High fatigue strength: The material can withstand repeated stress cycles encountered during drilling and production operations, minimizing the risk of premature failure. * Good weldability: Inconel 625 powder allows for strong and reliable welds, ensuring secure connections in pipelines and well components. |
해양 | * Propeller shafts * Rudder components * Heat exchangers for seawater systems * Desalination plants |
* Outstanding resistance to seawater corrosion: Inconel 625 powder is impervious to the detrimental effects of saltwater, preventing pitting, crevice corrosion, and biofouling, which can compromise structural integrity and functionality. * High mechanical strength: Even in cold ocean depths, Inconel 625 powder maintains its strength, ensuring reliable performance of critical marine components. * Hydrolysis resistance: The material is resistant to the breakdown caused by seawater, safeguarding the integrity of equipment used in desalination processes. |
화학 처리 | * Reaction vessels * Heat exchangers * Distillation columns * Transfer piping * Valves for handling corrosive chemicals |
* Exceptional resistance to a wide range of chemicals: Inconel 625 powder can withstand exposure to harsh acids, alkalis, and oxidizing agents, making it ideal for containment and processing equipment in the chemical industry. * High creep resistance at elevated temperatures: The material retains its shape under sustained stress and high heat, ensuring safe and efficient chemical reactions. * Good fabricability: Inconel 625 powder can be formed into complex shapes using additive manufacturing techniques, enabling the creation of customized components for specific chemical processing needs. |
오염 관리 | * Flue gas desulfurization (FGD) systems * Scrubber equipment handling corrosive gases * High-temperature filters |
* Superior resistance to sulfur compounds and acidic environments: Inconel 625 powder effectively resists the corrosive effects of sulfur dioxide and other acidic gases present in flue gas, ensuring the long-term durability of pollution control equipment. * High-temperature oxidation resistance: The material maintains its integrity at the elevated temperatures encountered in FGD systems, enabling efficient and reliable operation. * Good weldability: Allows for strong and secure connections in complex pollution control equipment. |
인코넬 625 분말의 사양 및 등급
사양 | 설명 | 일반 값 | 단위 | Importance for Additive Manufacturing |
---|---|---|---|---|
화학 성분 | The elemental makeup of Inconel 625 powder, crucial for achieving its advantageous properties. | |||
니켈(Ni) | Minimum content ensures good ductility and forms the base of the alloy. | ≥ 58% | wt% | Provides a strong, formable matrix for the other elements. |
크롬(Cr) | Range dictates oxidation resistance and high-temperature strength. | 20-23% | wt% | Creates a protective chromium oxide layer at elevated temperatures. |
철(Fe) | Maximum level controls mechanical properties and cost. | ≤ 5% | wt% | Contributes to strength and keeps the material cost-effective. |
몰리브덴(Mo) | Range influences corrosion resistance, especially in high-chloride environments. | 8-10% | wt% | Enhances resistance to pitting and crevice corrosion. |
니오븀(Nb) | Specific range promotes high-temperature strength and creep resistance. | 3.15-4.15% | wt% | Strengthens the grain boundaries and improves performance at elevated temperatures. |
코발트 (Co) | Maximum level refines grain size and improves high-temperature strength. | ≤ 1% | wt% | Contributes to strength and refines the microstructure. |
실리콘(Si) | Maximum limit controls fluidity and castability. | ≤ 0.50% | wt% | Minimizes casting defects and improves powder flow. |
Phosphorus (P) & Sulfur (S) | Combined maximum content ensures good weldability and ductility. | ≤ 0.15% | wt% | Prevents embrittlement during welding and maintains good mechanical properties. |
입자 크기 분포 | The range of particle diameters in the powder, impacting flowability, packing density, and final part properties. | Varies based on application | μm | |
Dv10 | Diameter at which 10% of the particles are smaller. | μm | Affects powder flow and packing density, influencing surface finish and printability. | |
Dv50 | Median particle diameter. | μm | Determines packing density and influences mechanical properties of the final part. | |
Dv90 | Diameter at which 90% of the particles are smaller. | μm | Impacts layer thickness and influences surface roughness of the final part. | |
입자 형태학 | The shape of the powder particles, affecting packing density, flowability, and printability. | Typically spherical | – | |
구형성 | Ratio of a particle’s diameter to its equivalent sphere’s diameter. | ≥ 0.90 | – | Spherical particles flow better, pack more densely, and improve laser penetration during printing. |
유동성 | The ease with which powder flows, critical for consistent layer formation in additive manufacturing processes. | Measured by various techniques | g/s | Good flowability ensures smooth powder feeding and minimizes printing defects. |
겉보기 밀도 | The mass of powder per unit volume, influencing powder handling and bed density during printing. | Varies based on particle size and morphology | g/cm³ | Affects powder usage and influences the density of the final printed part. |
탭 밀도 | The density of powder after a standardized tapping routine, indicating packing efficiency. | Higher density preferred | g/cm³ | Higher tap density signifies better packing and improves the mechanical properties of the final part. |
성적 | Different specifications for Inconel 625 powder based on particle size and other properties. | ASTM B446, AMS 5599, AMS 5666 | – | |
ASTM B446 | Standard specification for Inconel 625 powder used in various applications. | – | – | General-purpose grade suitable for a wide range of additive manufacturing processes. |
AMS 5599 & 5666 | Aerospace Material Specifications for Inconel 625 powder with tighter control on chemistry and particle characteristics. | – | – | Grades meeting stricter requirements for critical aerospace applications. |
인코넬 625 분말 가격
Inconel 625 powder, a nickel-based superalloy prized for its exceptional strength, corrosion resistance, and high-temperature performance, is a vital material in additive manufacturing (3D printing) and other industrial applications. Understanding Inconel 625 powder pricing requires considering several factors:
팩터 | 설명 | 가격에 미치는 영향 |
---|---|---|
수량 | The amount of Inconel 625 powder purchased significantly affects the price per unit weight. Suppliers typically offer tiered pricing, with lower per-gram costs for larger quantities. | Larger quantities generally result in a lower price per gram. |
입자 크기 및 형태 | The size and shape of the Inconel 625 powder particles influence printability, material properties of the finished product, and powder handling requirements. | Spherically shaped powders with a narrow particle size distribution are generally more expensive due to the additional processing involved. |
화학 성분 | Minor variations in the chemical makeup can optimize Inconel 625 powder for specific applications, such as those requiring maximum strength or corrosion resistance. | Powders with a tighter chemical specification may come at a premium. |
공급업체 | The reputation, geographic location, and production capacity of the supplier can influence pricing. | Reputable suppliers with stringent quality control measures may command higher prices. |
애플리케이션 | The intended use of the Inconel 625 powder can influence pricing. For instance, powders for aerospace applications may undergo more rigorous testing, impacting cost. | Powders intended for critical applications may be more expensive. |
구입처 인코넬 625 분말
Inconel 625 powder, a superhero among metal powders with its high-temperature resilience, corrosion-fighting abilities, and superior strength, is a cornerstone of additive manufacturing and various industrial applications. However, its price isn’t a one-size-fits-all situation. Delving into the world of Inconel 625 powder pricing requires examining several key factors, like a detective case:
팩터 | The Intricate Web | How it Affects the Price Tag |
---|---|---|
Quantity: The Balancing Act | Whether you’re needing a thimbleful or a treasure chest full, the amount of Inconel 625 powder you purchase significantly impacts the price per unit weight. Suppliers often have tiered pricing structures, offering a lower price per gram for those who buy in bulk. | The more powder you buy, the lower the price per gram typically goes. |
Particle Size and Morphology: The Powder’s Fingerprint | Imagine the Inconel 625 powder particles – are they uniform spheres or an uneven cast of characters? The size and shape (morphology) of these particles influence how easily they can be 3D printed, the final product’s properties, and how they need to be handled. | Spherically shaped powders with a narrow range of particle sizes are generally more expensive due to the extra processing involved in achieving this consistency. |
Chemical Composition: A Recipe for Performance | While the core ingredients of Inconel 625 powder remain the same, slight variations in its chemical makeup can be made to optimize it for specific applications. For example, some applications might require the powder to have the absolute maximum strength, while others might prioritize top-notch corrosion resistance. | Powders with a more precise chemical composition may come at a premium price. |
Supplier: The Source of the Spark | The reputation, location on the map, and production capacity of the supplier you choose can all influence pricing. Suppliers known for their stringent quality control measures may command higher prices, but you’re also getting the guarantee of a high-quality product. | Reputable suppliers with a proven track record of quality might have higher prices compared to others. |
The Powder’s Purpose: A Journey Defined | What grand adventure awaits the Inconel 625 powder you purchase? The intended application can influence pricing. For instance, powders destined for use in critical aerospace applications might undergo more rigorous testing, adding to the cost. | Powders designed for demanding applications, like aerospace, may be more expensive. |
인코넬 625 분말의 장단점
기능 | 장점 | 단점 |
---|---|---|
고온 성능 | * 탁월한 힘: Inconel 625 powder retains its structural integrity and strength at extremely high temperatures, exceeding 1800°F (982°C). This makes it ideal for applications in aerospace (turbine blades, exhaust components), power generation (heat exchangers, combustors), and other industries encountering intense heat. * 산화 저항: The carefully formulated blend of elements in Inconel 625 powder grants it superior resistance to oxidation. This prevents the material from degrading or weakening at high temperatures, ensuring long-lasting performance in hot, oxygen-rich environments. |
* High Material Cost: Nickel-based superalloys like Inconel 625 are inherently more expensive than commonly used materials like steel or aluminum. The cost of the powder itself is high, and specialized printing processes can further inflate production costs. |
내식성 | * Broad Spectrum Protection: Inconel 625 powder boasts exceptional resistance to a wide range of corrosive environments. It excels in applications exposed to seawater, harsh chemicals (acids, alkalis), and other aggressive media. This makes it a valuable material for the chemical processing industry, marine engineering, and applications involving fluid handling. | * Not Universally Resistant: While highly resistant, Inconel 625 powder does have limitations. Certain molten salts and specific highly concentrated acidic environments can cause corrosion. Careful material selection based on the exact operating conditions is crucial. |
설계 유연성 | * Additive Manufacturing (AM) Compatibility: Inconel 625 powder shines in additive manufacturing (3D printing) due to its good weldability and flow characteristics. This allows for the creation of complex geometries and intricate designs that wouldn’t be possible with traditional manufacturing techniques. AM opens doors for lightweight, high-performance components in various industries. * Potential for Micro-cracking: The 3D printing process can introduce residual stresses and micro-cracks in the finished part if printing parameters aren’t optimized. Careful control of factors like laser power, scan strategy, and post-processing techniques (stress relieving, hot isostatic pressing) is essential to achieve desired mechanical properties. |
|
가공성 | * Spark Erosion and Laser Compatibility: Inconel 625 powder exhibits good machinability with spark erosion and laser cutting techniques. This enables the creation of intricate features and tight tolerances on the finished parts, reducing the need for extensive post-processing. | * 작업 강화: Inconel 625 powder can work harden during machining, making it progressively more difficult to machine further. This necessitates the use of specialized cutting tools and techniques to maintain efficiency and avoid tool wear. |
기타 속성 | * High Toughness: Inconel 625 powder offers superior toughness compared to many other materials. This translates to a lower risk of catastrophic failures and enhances the material’s resistance to impact and stress. * 용접성: Similar to its machinability, Inconel 625 powder possesses good weldability. This facilitates the joining of components made from the powder and allows for repairs to existing Inconel 625 parts, extending their service life. |
* Relatively High Density: While lighter than steel, Inconel 625 powder is denser than some materials used in AM, such as titanium or aluminum. This can be a consideration in applications where weight reduction is a critical factor. |
스테인리스 스틸 316L 파우더와 비교
속성 | 인코넬 625 | SS 316L |
---|---|---|
밀도 | 8.44g/cm3 | 7.9g/cm3 |
융점 | 2330°F(1276°C) | 2550°F(1399°C) |
인장 강도 | 125,000 psi | 82,700 psi |
수율 강도 | 100,000 psi | 30,000 psi |
신장 | 35% | 40% |
내식성 | 우수 | 매우 좋음 |
내열성 | 최대 1800°F까지 우수 | 최대 1500°F까지 양호 |
비용 | 높음 | 낮음 |
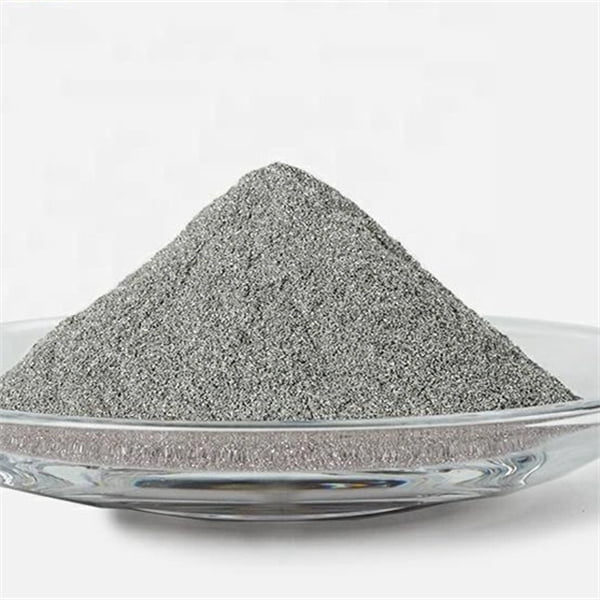
자주 묻는 질문
Q: Is 인코넬 625 분말 DMLS 또는 SLM 3D 프린팅에 적합합니까?
A: 예, 인코넬 625는 복잡한 형상과 우수한 재료 특성을 가진 고밀도 기능성 금속 부품을 제작할 수 있는 DMLS 및 SLM과 같은 레이저 분말 베드 용융 기술로 가공성이 뛰어납니다.
Q: 인코넬 625 파우더는 열처리가 필요합니까?
A: 대부분의 적층 제조된 인코넬 625 부품은 전용 열처리가 필요하지 않으며 서포트를 제거한 후 바로 사용할 수 있습니다. HIP는 물성 개선에 도움이 됩니다. 용액 어닐링, 에이징 처리도 옵션입니다.
Q: 인코넬 625 분말을 인쇄하는 데 가장 적합한 입자 크기는 무엇입니까?
A: DMLS/SLM 공정의 경우 15~45미크론 범위의 인코넬 625 분말은 확산성, 흐름 및 해상도 간에 균형이 잘 맞습니다. 매우 섬세한 특징이 있는 부품에는 10미크론 이하의 더 미세한 파우더를 사용해 볼 수 있습니다.
Q: 인코넬 625는 스테인리스 스틸보다 더 강합니까?
A: 예, 인코넬 625는 모든 온도에서 어떤 등급의 스테인리스강보다 훨씬 높은 강도를 제공하며 부식 성능도 훨씬 우수합니다. 하지만 가격도 더 비쌉니다.
Q: 인코넬 625는 바닷물에서 녹이 슬나요?
A: 아니요. 인코넬 625는 크롬과 니켈 함량이 높아 염화물로 인한 바닷물 환경의 구멍 및 틈새 부식에 대한 저항성이 뛰어나 해양 분야에 적합합니다.