Have you ever marveled at the sheer power and efficiency of a jet engine roaring to life? The relentless thrust that propels airplanes across continents or the incredible energy generation of industrial gas turbines – it’s all thanks to a symphony of meticulously engineered components. But hidden within these marvels of machinery lies a secret ingredient: gas turbine engineering powders. These fine, metallic particles play a critical role in crafting the very heart of these engines – the turbine disks and blades.
Imagine a tiny, metallic universe. Each gas turbine engineering powder particle is a microscopic warrior, specifically designed to withstand the brutal environment within a gas turbine. Here, scorching temperatures, immense pressure, and relentless centrifugal forces combine to create a battleground for materials. And that’s where these specially formulated powders come in, offering a unique combination of strength, heat resistance, and fatigue resistance – the holy trinity for gas turbine components.
But gas turbine engineering powders are not a one-size-fits-all solution. Just like a master chef wouldn’t use the same spice for every dish, engineers have developed a variety of powder types, each with its own distinct properties tailored for specific applications. Let’s delve deeper and explore this fascinating realm of metallic marvels.
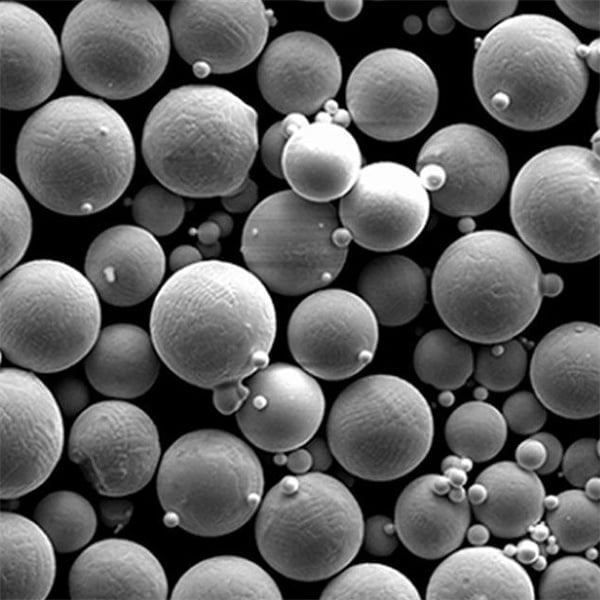
특성 가스터빈 엔지니어링 파우더
특성 | 설명 |
---|---|
머티리얼 구성 | Primarily nickel-based superalloys, but can also include cobalt and iron-based alloys |
입자 크기 및 분포 | Carefully controlled to optimize packing density and mechanical properties. Typically ranges from 10 to 150 microns |
모양 | Spherical for optimal flow and packing during consolidation |
유동성 | Plays a crucial role in additive manufacturing processes. Powders are engineered for smooth, consistent flow |
순도 | Strict control over impurities like oxygen, carbon, and sulfur is essential for optimal performance |
A Gallery of Powerhouse Powders
Now, let’s meet some of the key players in the world of gas turbine engineering powders:
- IN718: A workhorse material known for its excellent balance of strength, toughness, and fabricability. Consider it the all-rounder, adept at handling a variety of gas turbine applications.
- Rene 41: This high-performance alloy boasts superior creep resistance at elevated temperatures, making it ideal for hot sections of the turbine. Imagine it as the fireproof fighter, holding its ground against the scorching heat.
- CMS 247LC: This nickel-based superalloy offers exceptional resistance to oxidation and hot corrosion. Think of it as the shield bearer, deflecting the relentless assault of hot gases.
- Mar-M 247: This powerhouse material shines in applications demanding high strength and creep resistance at very high temperatures. It’s the ultimate gladiator, thriving in the harshest environments.
- AM 1624: A relative newcomer, this advanced alloy is specifically designed for additive manufacturing processes like 3D printing. Imagine it as the tech-savvy warrior, wielding the latest technology in the battle for performance.
- Astroloy: This cobalt-based superalloy offers exceptional high-temperature strength and oxidation resistance. Think of it as the champion in extreme environments, pushing the boundaries of what’s possible.
- DZ 125: This iron-based superalloy provides a cost-effective alternative for applications where ultimate performance isn’t the sole priority. It’s the strategic general, offering a good balance of value and capability.
- SRene 10X: This nickel-based superalloy boasts exceptional resistance to low-cycle fatigue, making it ideal for components that experience repeated stress cycles. Imagine it as the tireless warrior, enduring the constant strain of operation.
- PWA 1430: This advanced alloy offers superior creep resistance and high-temperature strength. Imagine it as the cutting-edge soldier, equipped with the latest advancements in materials science.
- Rene N5: This nickel-based superalloy is known for its excellent resistance to thermal fatigue and creep. Think of it as the adaptable warrior, performing well under varying temperature conditions.
Advantages of Gas Turbine Engineering Powders
이점 | 설명 | 혜택 |
---|---|---|
Enhanced Material Properties | Gas turbine engineering powders are produced through meticulously controlled processes like gas atomization, resulting in powders with exceptional purity, grain size distribution, and spherical morphology. These precisely engineered powders can be used to manufacture components with superior strength, creep resistance, fatigue resistance, and high-temperature performance compared to conventionally cast components. | This translates to increased efficiency and durability of gas turbine engines. Stronger components can withstand higher operating temperatures and pressures, leading to improved fuel efficiency and power output. Additionally, the improved creep resistance allows for longer service life before component replacement is needed, reducing maintenance costs. |
설계 유연성 | Powder-based manufacturing techniques like additive manufacturing (AM), also known as 3D printing, unlock new possibilities for gas turbine design. Unlike traditional casting methods limited by mold geometries, AM allows for the creation of complex internal features and intricate lattice structures. This design freedom enables engineers to optimize component weight for better fuel efficiency and create components with superior cooling channels for improved thermal management. | This flexibility fosters innovation in gas turbine design, pushing the boundaries of performance and efficiency. Optimized components can lead to lighter engines for aircraft applications or more compact designs for industrial power generation. |
Material Utilization | Powder-based manufacturing processes boast minimal material waste compared to conventional casting techniques. In casting, significant material is lost during the gating and sprue removal process. Conversely, with AM, unused powder can be recycled and reused, minimizing material waste and production costs. | This advantage promotes sustainability in gas turbine manufacturing. Reduced material consumption translates to lower environmental impact and aligns with growing demands for eco-friendly industrial practices. |
Reduced Lead Time | Additive manufacturing offers significant advantages in terms of lead time for producing complex gas turbine components. Since AM eliminates the need for complex mold creation, it allows for faster turnaround times compared to traditional casting methods. This rapid prototyping capability is crucial for developing and testing new gas turbine designs efficiently. | This translates to faster development cycles and quicker time-to-market for new and improved gas turbine technologies. This agility is particularly beneficial for the aerospace industry, where rapid innovation is critical. |
맞춤형 머티리얼 속성 | Powder metallurgy techniques enable the creation of novel materials with properties specifically tailored for gas turbine applications. By precisely controlling the composition and distribution of elements within the powder particles, engineers can create materials with optimized combinations of strength, ductility, and oxidation resistance. | This targeted approach to material design allows for the development of gas turbine components that can withstand the ever-increasing demands of higher operating temperatures and pressures. Additionally, it opens doors for the exploration of new material combinations that may not be achievable through conventional casting methods. |
Conformal Cooling | Additive manufacturing allows for the creation of complex internal cooling channels within gas turbine components. These channels can be designed to conform to the exact geometry of the component, ensuring optimal heat transfer and reducing thermal gradients. This precise cooling strategy minimizes the risk of hot spots and thermal distortion, leading to improved component performance and lifespan. | This translates to more efficient operation and reliable performance of gas turbines. By maintaining cooler component temperatures, the risk of material degradation and component failure is minimized. |
경량화 | The design freedom offered by AM enables the creation of lighter gas turbine components with internal lattice structures. These intricate structures provide the necessary strength while minimizing weight, a crucial factor for aircraft gas turbines. Lighter components translate to improved fuel efficiency and increased aircraft range. | This benefit is particularly significant for the aerospace industry, where every kilogram saved translates to significant fuel savings and increased payload capacity. The ability to create lightweight, high-performance components is a major advantage of gas turbine engineering powders. |
단점 가스터빈 엔지니어링 파우더
단점 | 설명 | 영향 |
---|---|---|
High Powder Cost | Gas turbine engineering powders are often produced through complex and energy-intensive processes like gas atomization. This translates to a higher cost per kilogram compared to conventionally produced materials like wrought alloys. Additionally, the stringent quality control requirements for these powders further contribute to their premium pricing. | The high cost of powders can significantly increase the overall manufacturing cost of gas turbine components. This can be a major hurdle for widespread adoption, particularly for cost-sensitive applications in the power generation industry. |
프로세스 복잡성 | Additive manufacturing, the primary processing technique for gas turbine engineering powders, is a relatively new technology compared to traditional casting methods. While offering design freedom, AM processes can be complex and require specialized expertise to operate effectively. Factors like powder selection, laser parameter optimization, and post-processing techniques all play a crucial role in the success of the build. | The complexity of AM processes can pose challenges for manufacturers, especially those lacking experience with this technology. Improper process control can lead to defects like porosity, poor mechanical properties, and dimensional inaccuracies in the final component. |
제한된 빌드 크기 | Current AM machines have limitations on the size of components they can produce. While large-scale AM machines are under development, they are not yet widely available. This restricts the application of gas turbine engineering powders to smaller components within a gas turbine engine. | This limitation can be a barrier for the use of AM in manufacturing large gas turbine components like turbine discs or combustor liners. It necessitates reliance on conventional casting methods for these larger, critical components. |
분말 처리 | Gas turbine engineering powders are often susceptible to moisture and oxygen contamination. These contaminants can adversely affect the flowability of the powder during the AM process and can lead to the formation of defects like oxides within the final component. Stringent handling procedures and controlled environments are necessary to maintain powder quality and prevent contamination. | The meticulous handling requirements can add complexity and cost to the overall manufacturing process. Specialized equipment like inert gas enclosures and dehumidifiers might be needed to ensure proper powder storage and handling. |
Part Qualification | Gas turbine components are subject to rigorous safety and performance regulations. Since AM is a relatively new technology, qualifying AM-produced components for use in gas turbines can be a challenging and time-consuming process. Extensive testing and characterization are often required to demonstrate that the AM-produced component meets the stringent performance and safety standards demanded by regulatory bodies. | The lengthy qualification process can hinder the adoption of AM for gas turbine applications. Manufacturers might be hesitant to invest in this technology due to the uncertainty and potential delays associated with component qualification. |
표면 거칠기 | Components produced through AM can exhibit a characteristic surface roughness compared to conventionally cast components. This surface roughness can impact aerodynamic performance and increase the risk of fatigue crack initiation in high-stress areas. Post-processing techniques like machining and polishing can be employed to improve surface finish, but these add additional steps and costs to the manufacturing process. | The inherent surface roughness of AM components can be a disadvantage for certain gas turbine applications, particularly those with high aerodynamic requirements like compressor blades. Careful consideration of the impact of surface roughness on component performance is crucial during the design phase. |
Limited Material Availability | The range of materials currently available as gas turbine engineering powders is still under development compared to the vast selection of wrought alloys used in conventional manufacturing. This limited material selection can restrict design options for engineers seeking to optimize component performance for specific applications. | The restricted material selection can pose a challenge for pushing the boundaries of gas turbine performance. The development of new powder compositions with properties tailored for extreme operating conditions is an ongoing area of research. |
Applications of Gas Turbine Engineering Powders
애플리케이션 | 설명 | 혜택 |
---|---|---|
터빈 블레이드 | The complex geometries of turbine blades, particularly those in the high-pressure section, can be readily produced using AM with gas turbine engineering powders. These intricate internal cooling channels optimize heat transfer and improve blade efficiency. Additionally, AM allows for the creation of blisk designs, where the blade and disk are manufactured as a single unit, reducing weight and simplifying assembly. | This translates to improved efficiency and performance of the gas turbine engine. Optimized cooling channels minimize thermal gradients within the blade, reducing the risk of hot spots and thermal distortion. Additionally, blisk designs offer weight reduction benefits, particularly crucial for aircraft gas turbines. |
Combustor Liners | The ability to create intricate internal features with AM makes gas turbine engineering powders well-suited for combustor liners. These liners play a critical role in fuel mixing and flame stabilization within the combustor. AM allows for the design of complex swirlers and flame holders that promote efficient fuel-air mixing and minimize pollutant emissions. | This contributes to cleaner and more efficient combustion within the gas turbine. Precise control over swirler and flame holder geometry enables optimized fuel-air mixing, leading to improved combustion efficiency and reduced emissions of pollutants like NOx. |
열교환기 | The high-temperature capabilities and design flexibility offered by gas turbine engineering powders make them ideal for heat exchanger applications within gas turbines. AM allows for the creation of highly efficient heat exchangers with complex internal geometries that maximize heat transfer surface area. These advanced heat exchangers can improve the overall thermal efficiency of the gas turbine cycle. | This translates to increased power output and fuel savings for the gas turbine. The ability to create intricate internal flow paths within the heat exchanger optimizes heat transfer, leading to improved cycle efficiency and reduced fuel consumption. |
Lightweight Components | The design freedom offered by AM, combined with the high strength-to-weight ratio of some gas turbine engineering powders, enables the creation of lightweight components for gas turbines. This is particularly beneficial for aircraft gas turbine engines, where weight reduction directly translates to improved fuel efficiency and increased range. Components like compressor housings and structural brackets can be optimized for both strength and weight using AM. | This contributes to significant fuel savings and increased operational range for aircraft powered by gas turbine engines. The ability to create lightweight, high-performance components is a major advantage for aircraft applications. |
Advanced Cooling Designs | Gas turbine engineering powders enable the creation of advanced cooling channels within gas turbine components. These channels can be conformal to the exact geometry of the component, ensuring optimal heat transfer and reducing thermal gradients. This allows for the operation of gas turbines at higher temperatures and pressures, improving overall efficiency and power output. | This pushes the boundaries of gas turbine performance. By enabling efficient cooling strategies, AM facilitates the use of advanced materials that can withstand higher operating temperatures, leading to increased efficiency and power output. |
신속한 프로토타이핑 | The ability to rapidly iterate on designs using AM with gas turbine engineering powders makes it a valuable tool for rapid prototyping of gas turbine components. This allows engineers to quickly test and refine new designs before committing to large-scale production runs. This rapid development cycle accelerates innovation in gas turbine technology. | This shortens development times and reduces costs associated with bringing new gas turbine technologies to market. The ability to quickly prototype and test new designs is crucial for staying ahead of the curve in a rapidly evolving industry. |
Repair of Critical Components | Gas turbine engineering powders can be used for repairing critical gas turbine components. AM allows for localized deposition of material to rebuild damaged areas or fill in eroded surfaces. This minimizes the need for complete component replacement, reducing downtime and maintenance costs. | This contributes to increased uptime and reduced maintenance costs for gas turbine operators. The ability to repair critical components extends their service life and avoids the need for expensive replacements. |
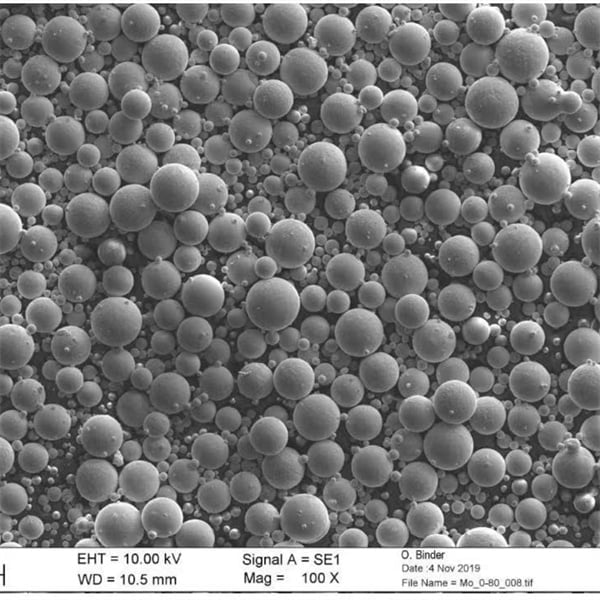
Typical Specifications, Sizes, Grades, and Standards:
기능 | 설명 |
---|---|
머티리얼 구성 | Varies depending on the specific powder type. Chemical composition is typically controlled to strict specifications as outlined by relevant standards |
입자 크기 및 분포 | Typically ranges from 10 to 150 microns, with specific ranges depending on the application and desired properties. Particle size distribution is carefully controlled for optimal packing density. |
모양 | Spherical for optimal flow and packing during consolidation processes. |
유동성 | Measured using standardized tests to ensure consistent and smooth powder flow during additive manufacturing processes. |
순도 | Strict control over impurities like oxygen, carbon, and sulfur is essential for optimal performance. Limits are defined by relevant standards. |
성적 | Different powder grades may be available depending on the specific alloy and manufacturer. These grades may vary in terms of minor element composition or processing parameters. |
표준 | Gas turbine engineering powders typically adhere to industry standards set by organizations like ASTM International (ASTM) or AMS International (AMS). These standards define specifications for material composition, particle size, and other critical parameters. |
공급업체 및 가격 세부 정보
Information | 설명 | 고려 사항 |
---|---|---|
공급업체 풍경 | The market for gas turbine engineering powders is relatively concentrated with a limited number of major players. These companies possess the expertise and infrastructure necessary to produce high-quality powders that meet the stringent requirements of the gas turbine industry. | Due to the complexity of the production process and the need for strict quality control, entry barriers for new suppliers are high. This can limit competition and potentially impact pricing. |
Examples of Key Suppliers | Some prominent suppliers of gas turbine engineering powders include: | * APEX Powder Company (USA) * Höganäs AB (Sweden) * AMETEK SMP (USA) |
가격 요소 | The pricing of gas turbine engineering powders is influenced by several factors, including: | * Powder Material: Exotic high-performance alloys typically come at a premium compared to more common nickel-based superalloys. * 파우더 순도: Powders with higher purity levels command a higher price due to the strict quality control measures required. * 입자 크기 및 형태: Powders with finer particle sizes and spherical morphologies are generally more expensive to produce and may cost more. * 주문 수량: Larger order volumes may qualify for discounted pricing from some suppliers. |
추가 고려 사항 | Beyond the base price of the powder, there are additional costs to consider when using gas turbine engineering powders for AM: | * 최소 주문 수량: Some suppliers may have minimum order quantities that can be a hurdle for smaller projects or prototyping applications. * 후처리 비용: Gas turbine components produced via AM may require post-processing steps like heat treatment, support removal, and surface finishing, which add to the overall manufacturing cost. |
시장 동향 | The market for gas turbine engineering powders is expected to grow in the coming years, driven by factors like: | * Increasing demand for more efficient and powerful gas turbines for power generation and aircraft propulsion. * Advancements in AM technology that are expanding the design possibilities for gas turbine components. * Growing focus on lightweighting aircraft to improve fuel efficiency and range. |
A Look at the Costs:
It’s important to note that specific pricing information for gas turbine engineering powders is often not publicly available due to commercial sensitivity. However, these powders are generally considered high-value materials compared to conventional options. The cost, however, needs to be weighed against the potential benefits they offer in terms of performance, design flexibility, and material utilization.
Comparing Powder-Based vs. Traditional Manufacturing Methods
When it comes to manufacturing gas turbine components, traditional methods like casting and machining from solid blocks have been the workhorses for decades. However, powder-based techniques are gaining significant traction due to several advantages:
- 우수한 머티리얼 속성: As mentioned earlier, powder metallurgy techniques can achieve superior strength, fatigue resistance, and creep resistance compared to traditional casting methods. This translates to increased efficiency and longer lifespans for gas turbines.
- 디자인 유연성: Powder-based additive manufacturing allows for the creation of complex geometries that are difficult or impossible to achieve with conventional machining. This opens doors for innovative and more efficient turbine designs, such as components with internal cooling channels or lighter weight structures.
- 향상된 재료 활용도: Powder-based processes offer minimal material waste compared to traditional methods like machining from solid blocks. This translates to cost savings and reduced environmental impact.
- 그물 모양에 가까운 제조: Powder-based additive manufacturing techniques can create components with near-net shapes, requiring minimal post-processing compared to traditional methods. This translates to faster production times and reduced costs.
However, traditional methods also have their own advantages:
- Lower upfront costs: Setting up traditional manufacturing processes typically requires a lower initial investment compared to powder-based additive manufacturing equipment.
- Established processes: Traditional methods have been around for decades, and the processes are well-established and understood. This can lead to higher production volumes and potentially lower production costs for high-volume components.
- Wider range of material options: Traditional methods can often handle a wider range of material types compared to powder-based methods, which are still under development for some alloys.
The choice between powder-based and traditional manufacturing methods depends on several factors, including:
- The specific component being manufactured: For complex geometries or components requiring superior material properties, powder-based methods may be the preferred choice.
- 생산량: For high-volume production runs, traditional methods may be more cost-effective.
- 자료 가용성: If a specific alloy is not readily available in powder form, traditional methods may be the only option.
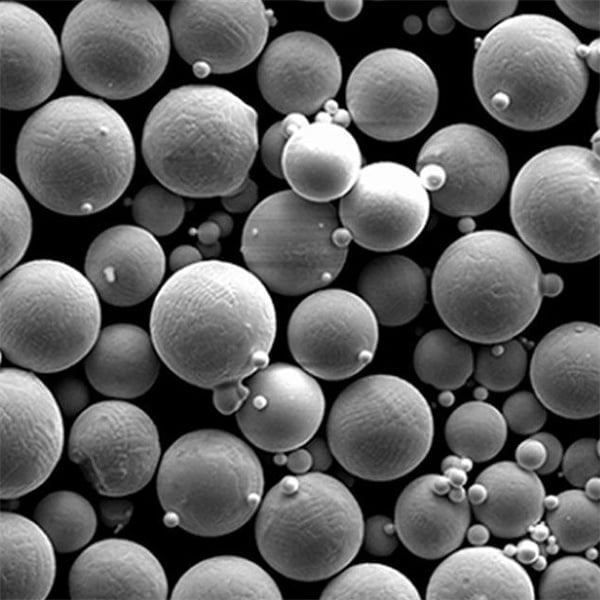
The Future of Gas Turbine Engineering Powders
The future of gas turbine engineering powders is bright. As additive manufacturing technology continues to advance, the demand for these specialized powders is expected to grow. Here are some exciting trends to watch:
- Development of new powder alloys: Researchers are constantly developing new powder alloys with even better performance characteristics for even higher efficiency and operational temperatures in gas turbines.
- 파우더 생산 방법이 개선되었습니다: Advancements in powder production techniques are leading to more cost-effective and efficient methods for manufacturing high-quality gas turbine engineering powders.
- Standardization of powder specifications: As the use of gas turbine engineering powders becomes more widespread, increased standardization of powder specifications and certifications will ensure consistent quality and performance.
자주 묻는 질문
질문 | 답변 |
---|---|
What are the main advantages of using gas turbine engineering powders? | Gas turbine engineering powders offer several advantages, including enhanced material properties, design flexibility, improved material utilization, and microstructure control. |
What are some of the disadvantages of using gas turbine engineering powders? | Disadvantages include higher cost compared to traditional materials, process complexity, and the need for strict quality control measures. |
What are the typical applications of gas turbine engineering powders? | These powders are primarily used in manufacturing turbine disks and blades, combustor liners, nozzle guide vanes, heat shields, and increasingly in various aerospace, automotive, and medical applications through additive manufacturing. |
What are some factors that influence the pricing of gas turbine engineering powders? | Material composition, particle size distribution, quantity, and adherence to specific standards can all impact pricing. |
How do powder-based manufacturing methods compare to traditional methods for gas turbine components? | Powder-based methods offer superior material properties, design flexibility, and improved material utilization, but come with higher upfront costs and process complexity. Traditional methods are more established and have a wider range of material options, but may be limited in design complexity and generate more waste. |
In conclusion, gas turbine engineering powders are playing a transformative role in the world of gas turbines. These microscopic marvels offer a unique combination of properties that are pushing the boundaries of performance and efficiency. As technology continues to evolve, we can expect even more exciting developments in the realm of these specialized powders, paving the way for a future of cleaner, more powerful, and efficient gas turbines.