개요 전자빔 용융
전자빔 용융(EBM)은 전자빔 전원을 사용하여 금속 분말 재료를 층별로 선택적으로 녹이고 융합하여 부품을 제작하는 적층 제조 공정입니다.
전자빔 용융에 대한 몇 가지 주요 세부 사항은 다음과 같습니다:
- 진공 상태에서 전자빔 건을 사용하여 분말을 녹입니다.
- 빌드는 고온에서 이루어지므로 층간 결합이 잘 이루어집니다.
- 주로 Ti, Ni, Co 합금 및 기타 고성능 소재에 사용됩니다.
- 기존 방식과 동등하거나 그 이상의 속성을 가진 거의 풀 밀도 부품을 제공합니다.
- 기존 제작 방식으로는 불가능한 복잡한 형상을 지원합니다.
- 항공우주, 의료 및 자동차 산업에서 일반적으로 사용됩니다.
- 전자빔 적층 제조(EBAM) 또는 전자빔 자유형 제조(EBF3)라고도 합니다.
전자빔 용융 장비
유형 | 설명 |
---|---|
전자 빔 건 | 고에너지 빔을 생성하고 집중시켜 재료를 녹입니다. 핵심 구성 요소입니다. |
파우더베드 | 블레이드 또는 롤러로 긁어낸 파우더 층이 포함되어 있습니다. 이동식 플랫폼에 구축되었습니다. |
진공 챔버 | 빌드하는 동안 전체 시스템이 진공 상태입니다. 빔 초점에 매우 중요합니다. |
제어 시스템 | 소프트웨어 슬라이스 및 제어 빌드 파라미터. 인프로세스 모니터링 및 제어 기능을 제공합니다. |
처리 시스템 | 부품을 적재/하역하고 사용하지 않은 분말을 재활용하는 데 사용됩니다. |
차폐 | 엑스레이 발생으로 인해 챔버 주변에 납 차폐가 필요합니다. |
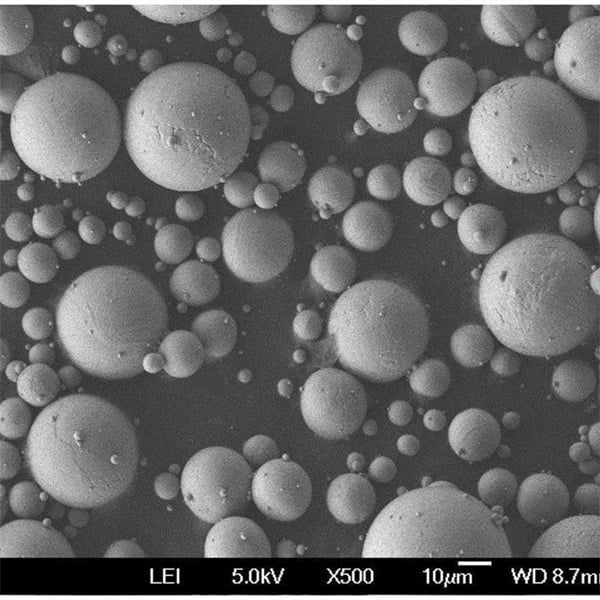
사용되는 재료 전자빔 용융
재질 | 주요 속성 | 일반적인 애플리케이션 |
---|---|---|
티타늄 합금 | 높은 중량 대비 강도, 생체 적합성 | 항공우주, 의료용 임플란트 |
니켈 합금 | 내식성, 고강도 | 터빈, 로켓 부품 |
코발트-크롬 합금 | 경도, 내마모성/내식성 | 의료용 임플란트, 툴링 |
스테인리스 스틸 | 우수한 내구성, 손쉬운 처리 | 산업용 툴링, 금형 |
알루미늄 합금 | 가벼운 무게 | 항공우주, 자동차 |
귀금속 | 높은 화학적 불활성 | 쥬얼리, 의료 |
EBM은 출력 강도로 인해 레이저 기반 공정으로는 어려운 고성능 합금을 가공할 수 있습니다.
EBM 프로세스 사양
매개변수 | 일반적인 범위 |
---|---|
빔 파워 | 1-3 kW |
빔 전압 | 30-150kV |
빌드 크기 | 최대 200 x 200 x 350mm |
레이어 높이 | 50-200 μm |
빌드 속도 | 5-100 cm3/hr |
빔 크기 | 직경 0.1-1mm |
진공 레벨 | 5 x 10-4mbar |
빔 초점 | 0.1-0.5mm 스팟 크기 |
EBM 시스템을 사용하면 빔 출력, 속도, 초점 등의 파라미터를 조정하여 특정 재료에 맞게 조정할 수 있습니다.
EBM 시스템 공급업체
공급업체 | 주요 세부 정보 | 시작 가격 범위 |
---|---|---|
공급업체 1 | EBM 기술의 선구자. 가장 큰 설치 기반. | $1.2-$1.5백만 |
공급자 2 | 소형 부품용 시스템. 더 빠른 스캔 속도. | $0.8-$1.2백만 |
공급업체 3 | 연구 시스템. 개방형 매개변수 제어. | $0.5-$0.8 백만 |
시스템 비용은 빌드 볼륨, 빔 출력, 포함된 액세서리 및 소프트웨어 기능에 따라 달라집니다.
EBM 시스템 공급업체를 선택하는 방법
선택 기준 | 주요 고려 사항 | 설명 |
---|---|---|
공급업체 전문성 | 업계 지식 | 공급업체가 특정 업계에서 입증된 실적을 보유하고 있나요? 유사한 애플리케이션에 대한 경험을 통해 고객의 요구 사항과 잠재적인 문제를 더 깊이 이해할 수 있습니다. |
EBM 시스템 포트폴리오 | 공급업체는 어떤 범위의 EBM 시스템을 제공하나요? 예산, 복잡성, 원하는 기능에 맞는 포트폴리오를 갖춘 공급업체를 찾아보세요. | |
사용자 지정 기능 | 공급업체가 고유한 요구 사항에 맞게 EBM 시스템을 사용자 지정할 수 있나요? 여기에는 데이터 입력, 보고서를 맞춤화하거나 기존 소프트웨어와 통합하는 작업이 포함될 수 있습니다. | |
기술 역량 | 소프트웨어 기능 | EBM 시스템에서 제공하는 기능을 평가하세요. 시뮬레이션, 최적화 및 분석에 필요한 기능을 제공하나요? 모델 라이브러리, 시나리오 계획, 시각화 도구와 같은 기능을 고려하세요. |
확장성 | EBM 시스템이 현재와 미래의 요구 사항을 처리할 수 있나요? 비즈니스가 성장함에 따라 EBM 시스템은 더 복잡한 모델과 데이터 양을 수용할 수 있도록 조정되어야 합니다. | |
통합 기능 | EBM 시스템이 기존 소프트웨어 인프라와 원활하게 통합될 수 있나요? 원활한 통합은 원활한 데이터 흐름을 보장하고 수동 데이터 입력의 필요성을 없애줍니다. | |
구현 및 지원 | 구현 프로세스 | 공급업체가 잘 정의된 구현 프로세스를 제공하나요? 일정, 마일스톤, 교육 세션이 정의된 명확한 로드맵이 있는지 살펴보세요. |
기술 지원 | 공급업체는 어떤 수준의 기술 지원을 제공하나요? 기술적 문제를 효율적으로 해결할 수 있는 신속하고 지식이 풍부한 지원 인력을 갖춘 공급업체를 선택하세요. | |
사용자 교육 | 공급업체가 포괄적인 사용자 교육을 제공하나요? 교육을 통해 팀이 EBM 시스템을 효과적으로 활용하고 그 이점을 극대화할 수 있습니다. | |
공급업체 평판 및 신뢰성 | 재무 안정성 | 공급업체의 재무 상태를 조사하세요. 안정적인 회사일수록 지속적인 지원을 제공하고 장기적으로 EBM 시스템을 유지할 가능성이 높습니다. |
고객 참조 | 업계 내 기존 고객에게 추천서를 요청하세요. 만족한 고객과의 대화를 통해 공급업체의 역량과 서비스 품질에 대한 귀중한 인사이트를 얻을 수 있습니다. | |
업계 인정 | 공급업체가 EBM 시스템으로 업계 어워드나 인정을 받은 적이 있나요? 인정을 받았다는 것은 품질과 혁신에 대한 평판이 높다는 것을 의미합니다. | |
비용 및 가치 | 라이선스 비용 | 다양한 EBM 시스템의 라이선스 비용을 비교하세요. 시스템이 제공하는 가치와 잠재적인 투자 수익률(ROI)과 관련된 비용을 고려하세요. |
구현 비용 | 교육 및 필요한 사용자 지정 등 구현 비용을 고려하세요. | |
지속적인 지원 비용 | 지속적인 기술 지원 및 유지 관리와 관련된 비용을 이해합니다. |
최적화하는 방법 EBM 프로세스
팩터 | 설명 | 부품 품질에 미치는 영향 | 최적화 전략 |
---|---|---|---|
파우더 소재 | 입자 크기, 분포, 화학 | 용융 거동, 밀도 및 기계적 특성에 직접적인 영향을 미칩니다. | 균일한 포장과 흐름을 위해 크기 분포가 촘촘한 구형 분말을 사용합니다. 원하는 최종 부품 특성(예: 강도, 내식성)에 따라 분말 화학 물질을 선택합니다. 예열 또는 건조 절차를 실행하여 습기를 제거하고 유동성을 개선합니다. |
빔 파라미터 | 빔 파워, 스캔 속도, 스팟 크기, 스캔 패턴 | 용융 깊이, 열 구배 및 잔류 응력 제어 | 빔 출력과 스캔 속도를 미세 조정하여 과도한 스패터나 기화 없이 완전한 용융을 달성할 수 있습니다. 스캔 패턴(해치 간격, 스캔 회전)을 조정하여 열 집중과 뒤틀림을 최소화합니다. 빔 오프셋 기술을 활용하여 용융 중 수축을 보정합니다. |
빌드 환경 | 진공 압력, 챔버 온도 | 깨끗하고 통제된 분위기를 유지하고 산화를 줄입니다. | 가스 오염을 방지하기 위해 높은 진공 수준(일반적으로 10^-4 Pa)을 유지합니다. 챔버를 분말의 녹는점보다 약간 낮은 온도로 예열하여 유동성을 개선하고 열 충격을 줄입니다. |
지원 구조 | 디자인, 소재 | 적절한 열 방출을 보장하고 부품 붕괴 방지 | 재료 사용량과 후처리 시간을 최소화하기 위해 최소한의 지지 구조를 설계합니다. 복잡한 지오메트리에 격자 구조 또는 분리형 지지대를 활용하세요. 사후 처리를 간소화할 수 있는 대체 서포트 재료(예: 수용성 서포트)를 살펴보세요. |
프로세스 모니터링 및 제어 | 용융 풀 모니터링, 레이어 두께 제어 | 일관된 빌드 품질 보장 및 잠재적 결함 식별 | 실시간 용융 풀 모니터링 시스템(예: 고온 측정, 용융 풀 이미징)을 구현하여 최적의 용융 거동을 위해 공정 파라미터를 조정합니다. 폐쇄 루프 피드백 시스템을 사용하여 센서 데이터를 기반으로 레이어 두께를 자동으로 조정합니다. |
포스트 프로세싱 기법 | 열간 등방성 프레스(HIP), 가공, 표면 마무리 | 기계적 특성, 치수 정확도 및 표면 품질 향상 | HIP를 활용하여 내부 공극을 제거하고 부품 밀도를 높입니다. 잔류 응력을 최소화하고 피로 수명을 개선하기 위해 응력 완화 가공 기술을 구현합니다. 원하는 표면 특성에 따라 적절한 표면 마감 방법(예: 샷 피닝, 폴리싱)을 사용합니다. |
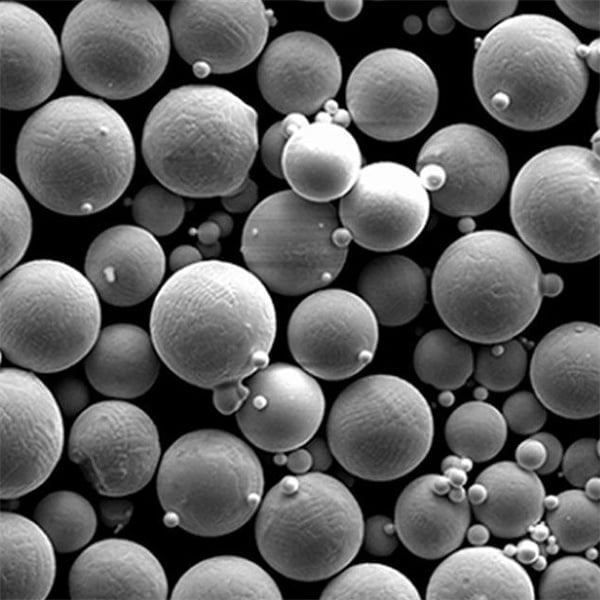
EBM용 부품 설계 방법
기능 | 설명 | EBM 혜택 | 고려 사항 |
---|---|---|---|
벽 두께 | 디자인에서 솔리드 피처의 최소 두께입니다. | 복잡한 세부 사항과 내부 채널을 활성화합니다. | 너무 얇으면(0.3mm 미만) 해상도가 떨어지고 균열이 생길 수 있습니다. 재료와 원하는 기계적 특성에 따라 최소 두께를 고려하세요. |
오버행 각도 | 피처가 지지대 없이 튀어나온 각도입니다. | 복잡한 지오메트리를 구현합니다. | 45°보다 가파른 각도는 일반적으로 지지 구조가 필요하므로 후처리가 증가하고 강도가 떨어질 가능성이 있습니다. 더 완만한 경사로 기능을 재설계하거나 오버행 지원을 위해 격자 구조를 활용하세요. |
내부 기능 | 부품 내의 채널, 캐비티 및 빈 섹션. | 무게를 가볍게 하고 유체 흐름이나 열 방출을 위한 공간을 만듭니다. | 인쇄 중 붕괴를 방지하기 위해 내부 피처의 벽 두께를 적절하게 유지합니다. 모서리가 둥근 채널로 설계하여 스트레스 집중 지점을 최소화합니다. 큰 내부 공동은 과도한 분말을 제거하기 위해 전략적으로 배수구를 배치해야 할 수 있습니다. |
초안 각도 | 수직 측벽의 테이퍼 각도입니다. | 파우더 제거가 쉬워지고 표면 거칠기가 줄어듭니다. | 대부분의 금속에는 최소 5~10°의 통풍을 권장합니다. 복잡한 피처나 깊은 구멍에는 더 가파른 드래프트가 필요할 수 있습니다. |
지원 구조 | 돌출된 피처를 지탱하기 위해 소프트웨어에서 생성한 임시 구조물입니다. | 자연스러운 빌드 각도를 넘어선 복잡한 지오메트리를 구현할 수 있습니다. | 지원 사용량을 최소화하여 사후 처리 시간과 잠재적인 지원 마크 제거 문제를 줄이세요. 가능한 한 자체 지원 기능을 설계하세요. 지지대가 필요한 경우 분리형 또는 용해형 지지대를 선택하면 쉽게 제거할 수 있습니다. |
격자 구조 | 내부적으로 무게를 줄이거나 맞춤형 강성을 위해 사용되는 개방형 셀 구조입니다. | 무게 대 강도 비율을 최적화하고 특정 기계적 특성을 달성합니다. | 원하는 하중 지지 특성에 따라 다양한 격자 유형(예: 큐빅, 다이아몬드)을 살펴보세요. 격자 내에서 적절한 스트럿 두께를 확보하여 구조적 무결성을 유지합니다. |
표면 마감 | 인쇄된 파트 표면의 최종 텍스처입니다. | 원하는 미적 또는 기능적 요구 사항을 달성합니다. | 인쇄된 EBM 표면은 약간 거칠 수 있습니다. 더 매끄러운 마감을 원한다면 가공 또는 연마와 같은 후처리 기술을 고려하세요. 돌출부를 최소화한 디자인 기능으로 광범위한 표면 마감의 필요성을 줄입니다. |
재료 선택 | 인쇄에 사용되는 금속 분말의 유형입니다. | 다양한 금속의 고유한 특성을 활용합니다. | 일반적인 EBM 재료로는 티타늄 합금, 인코넬, CoCr 등이 있습니다. 소재를 선택할 때는 강도, 내식성, 생체 적합성, 열적 특성 등의 요소를 고려하세요. |
열 관리 | 인쇄 중 열로 인한 왜곡을 최소화하는 전략. | 치수 정확도를 유지하고 잔류 응력을 줄입니다. | 벽 두께의 변화를 활용하여 열을 고르게 분산시킵니다. 내부 채널 또는 격자 구조를 통한 방열 경로를 설계합니다. 특정 영역의 열 집중을 최소화하는 스캔 경로 최적화와 같은 인쇄 전략을 살펴보세요. |
EBM 부품 후처리 방법
단계 | 설명 | 목적 | 기술 | 고려 사항 |
---|---|---|---|---|
디폴더링 | 첫 번째 필수 단계는 제작 부품을 둘러싼 결합되지 않은 금속 가루를 제거하는 것입니다. | 안전한 취급을 보장하고 오염을 방지하며 적절한 검사 및 후속 마무리를 가능하게 합니다. |
기계식 파우더 제거: 다양한 자동 및 수동 가루 제거 스테이션은 브러시, 압축 공기, 진동을 사용하여 가루를 제거합니다. 워터 제트: 고압 워터젯이 표면 거칠기를 최소화하면서 파우더를 조심스럽게 제거합니다. |
부품 형상과 재료 특성에 따라 파우더 제거 방법을 선택합니다. 예를 들어 복잡한 피처는 부드럽게 제거하기 위해 워터 제트가 필요할 수 있습니다. 기계식 가루 제거 시 적절한 환기와 먼지 수거가 이루어지도록 하세요. |
지지 구조 제거 | EBM 부품은 돌출된 피처가 무너지는 것을 방지하기 위해 인쇄 중에 임시 지지 구조가 필요한 경우가 많습니다. | 최종 부품을 손상시키지 않고 지지 구조물을 제거할 수 있습니다. |
와이어 EDM(방전 가공): 전기 스파크를 사용하여 지지 구조를 절단하는 정밀한 방법입니다. 연삭: 수동 또는 CNC 제어 연삭은 더 큰 지지 구조를 제거합니다. 화학 밀링: 화학 배스는 용해성 재료로 만든 지지 구조를 녹입니다. |
와이어 EDM은 높은 정확도를 제공하지만 복잡한 서포트의 경우 시간이 많이 소요될 수 있습니다. 연삭은 더 빠르지만 부품 손상을 방지하기 위해 숙련된 작업자가 필요합니다. 화학 밀링은 용해성 서포트가 있는 유사한 부품의 대량 배치에 적합합니다. |
표면 거칠기 감소 | EBM의 레이어별 인쇄에서 발생하는 고유한 계단식 효과로 인해 표면 질감이 거칠어집니다. | 부품의 심미성, 기능적 성능, 마찰 특성(마모 및 마찰)을 개선합니다. |
샌딩 및 연마제 텀블링: 연마재는 마찰을 통해 표면을 매끄럽게 만듭니다. 진동 마감: 부품을 미디어 베드에서 진동시켜 전체적인 표면을 개선합니다. 연마: 기계적 또는 전기 화학적 연마로 거울과 같은 마감 처리가 가능합니다. |
선택한 기술은 원하는 표면 마감과 형상에 따라 다릅니다. 샌딩은 평평한 표면에 효과적이며, 텀블링은 복잡한 모양에 적합합니다. 연마는 가장 매끄러운 마감을 얻을 수 있지만 치수가 변경될 수 있습니다. |
스트레스 풀기 | EBM 중 급격한 가열 및 냉각으로 인해 부품에 잔류 응력이 발생할 수 있습니다. | 뒤틀림, 갈라짐의 위험을 줄이고 치수 안정성을 향상시킵니다. | 열 어닐링: 부품을 특정 온도로 가열하고 제어된 시간 동안 유지하여 스트레스가 이완되도록 합니다. | 어닐링 파라미터는 소재와 부품 형상에 따라 달라집니다. 부적절한 어닐링은 기계적 특성에 부정적인 영향을 미칠 수 있습니다. 재료 전문가와 상담하는 것이 좋습니다. |
검사 및 품질 관리 | 마지막 단계에서는 완성된 부품이 치수 공차, 표면 마감 요구 사항을 충족하고 균열이나 결함이 없는지 확인합니다. | 부품이 설계 사양에 부합하는지 확인하고 기능을 보장합니다. |
치수 측정: 3차원 측정기(CMM)는 부품의 특징을 고정밀로 측정합니다. 표면 거칠기 측정: 프로파일로미터는 표면 텍스처를 정량화합니다. 비파괴 검사(NDT): X-레이 방사선 촬영 및 초음파 테스트와 같은 기술은 내부 균열 및 결함을 감지합니다. |
검사 계획은 인쇄 전에 다음을 기반으로 수립해야 합니다. |
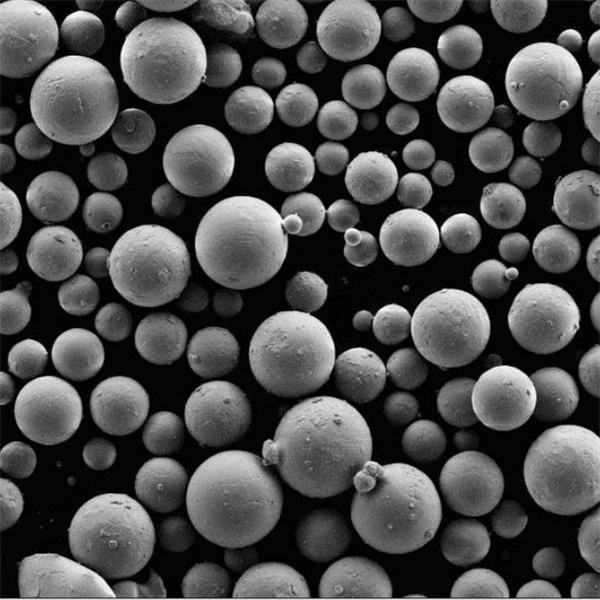
설치 및 통합 방법 EBM 부속
단계 | 작업 | 설명 | 고려 사항 |
---|---|---|---|
1 | 준비 | 설치를 시작하기 전에 원활한 통합 프로세스를 확인하세요. |
EBM 부품을 식별합니다: 통합하려는 근거 기반 의학(EBM) 구성 요소를 명확하게 정의하세요. 임상 의사 결정 지원 도구, 표준화된 프로토콜 또는 환자 교육 자료인가요? 시스템 호환성: EBM 부품과 기존 전자 건강 기록(EHR) 시스템 또는 플랫폼 간의 호환성을 확인합니다. 시스템마다 특정 파일 형식이나 통합 방법이 필요할 수 있습니다. 데이터 매핑: EBM 파트의 데이터를 EHR 시스템 내의 해당 필드에 매핑하는 방법을 계획하세요. 이렇게 하면 원활한 정보 흐름을 보장하고 데이터 중복을 방지할 수 있습니다. 워크플로 분석: 현재 워크플로우를 분석하여 EBM 파트 통합에 가장 적합한 지점을 파악하세요. 이를 통해 업무 중단을 최소화하고 사용자 채택을 최적화할 수 있습니다. |
2 | 설치 | EBM 부품 공급업체에서 제공하는 구체적인 지침을 따르세요. |
기술 전문성: EBM 부품의 복잡성에 따라 설치를 위해 IT 팀이나 EBM 부품 공급업체의 도움이 필요할 수 있습니다. 시스템 다운타임: 진행 중인 임상 활동의 중단을 최소화하기 위해 피크 시간이 아닌 시간대에 설치 일정을 잡으세요. 테스트: 설치 후 철저한 테스트를 수행하여 EBM 부품이 올바르게 작동하고 EHR 시스템과 원활하게 통합되는지 확인합니다. 다양한 시나리오를 테스트하여 잠재적인 문제를 파악하고 해결합니다. |
3 | 구성 | 특정 요구 사항과 워크플로에 맞게 EBM 부분을 조정할 수 있습니다. |
사용자 역할 및 권한: 사용자 역할을 정의하고 시스템 내 EBM 파트에 액세스하고 활용할 수 있는 적절한 권한을 할당하세요. 사용자 지정 옵션: EBM 파트에서 제공하는 사용자 지정 옵션을 살펴보세요. 여기에는 의사 결정 지원 프롬프트, 알림 임계값 또는 교육 콘텐츠를 환자 집단과 임상 진료에 더 적합하도록 조정하는 것이 포함될 수 있습니다. 보고 및 분석: 보고 기능을 구성하여 EBM 부품의 사용량과 영향을 추적할 수 있습니다. 이 데이터는 효과를 평가하고 추가 최적화를 위한 영역을 식별하는 데 유용할 수 있습니다. |
4 | 교육 및 지원 | 직원에게 EBM 부품을 효과적으로 활용할 수 있는 지식과 기술을 갖추도록 하세요. |
사용자 교육: 임상의와 직원을 위한 교육 자료를 개발하고 세션을 진행하여 EBM 부품의 기능, 이점 및 제한 사항을 숙지할 수 있도록 합니다. 지속적인 지원: EBM 부품 공급업체 또는 IT 팀으로부터 지속적인 지원을 받을 수 있는 명확한 채널을 구축하세요. 이렇게 하면 사용자가 어려움에 직면했을 때 쉽게 지원을 받을 수 있습니다. |
5 | 모니터링 및 평가 | EBM 부분의 효과를 지속적으로 평가하고 개선 기회를 파악하세요. |
성능 모니터링: EBM 부품 사용률, 프로토콜 준수, 환자 결과와 같은 주요 지표를 추적하세요. 사용자 피드백: 임상의와 직원으로부터 EBM 부품에 대한 경험에 관한 피드백을 수집합니다. 이를 통해 개선이 필요한 부분을 발견하거나 예상치 못한 이점을 강조할 수 있습니다. 데이터 분석: 모니터링 중에 수집된 데이터를 정기적으로 분석하여 추세를 파악하고 EBM 부품이 임상 진료 및 환자 치료에 미치는 영향을 평가합니다. |
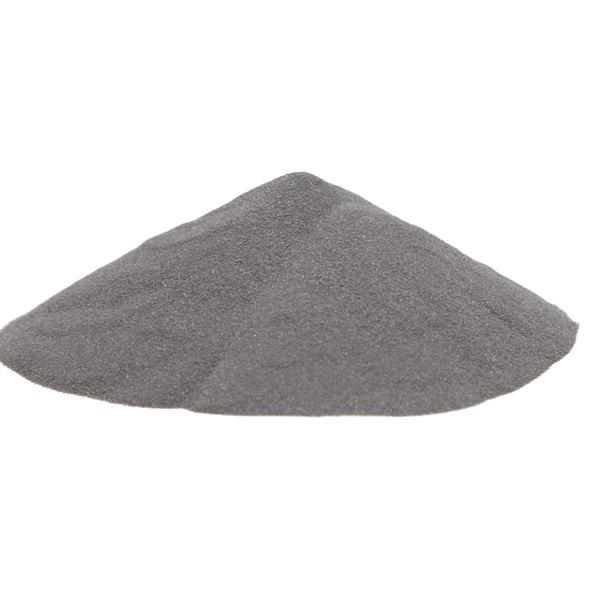
EBM 프린터 운영 및 유지보수
작업 | 설명 | 빈도 | 리소스 |
---|---|---|---|
미디어 로드 | 프린터 사양에 따라 올바른 용지 유형(라벨, 태그, 리본)이 로드되었는지 확인합니다. 용지를 급지함에 올바르게 정렬하여 용지가 똑바로 공급되고 장력이 적절한지 확인합니다. 최적의 핏을 위해 미디어 가이드를 조정합니다. |
각 인쇄 작업 전 | 프린터 설명서, 미디어 사양 |
리본 관리 | 리본의 마모 및 찢어짐을 점검합니다. 구겨지거나 닳았거나 수명이 다한 경우 교체하세요. 리본 유형(왁스, 수지 등)이 용지 및 인쇄 요구 사항과 일치하는지 확인합니다. |
각 인쇄 작업 전 또는 인쇄 품질이 저하되는 경우 | 리본 사양, 프린터 설명서 |
인쇄 작업 제출 | 인쇄 설정(해상도, 수량, 용지 크기, 방향)이 문서 사양과 일치하는지 확인합니다. 컴퓨터에서 적절한 프린터 드라이버를 선택합니다. 프린터로 보내기 전에 인쇄 작업을 미리 보고 정확성을 확인합니다. |
각 인쇄 작업 | 프린터 소프트웨어, 문서 작성 소프트웨어 |
인쇄 상태 모니터링 | 오류 또는 경고(용지 부족, 리본 문제, 프린트 헤드 문제)에 대한 프린터 알림을 관찰합니다. 프린터 출력물의 품질 문제(줄무늬, 얼룩, 정렬 불량)가 있는지 정기적으로 확인합니다. |
인쇄 중 | 프린터 디스플레이 패널, 인쇄 출력 |
매일 청소 | 보풀이 없는 천을 사용하여 프린터 외부 표면을 닦습니다. 이소프로필 알코올을 적신 면봉으로 프린트 헤드를 청소합니다(자세한 지침은 설명서 참조). |
매일 | 보풀이 없는 천, 이소프로필 알코올(매뉴얼의 권장 농도), 프린터 설명서 |
예약된 유지 관리 | 인쇄 경로(롤러, 플래튼)를 주기적으로 청소하려면 제조업체의 권장 사항을 따르세요. 마모된 프린트 헤드 또는 기타 구성품은 프린터 설명서의 지침에 따라 필요에 따라 교체합니다. |
3~6개월마다(또는 매뉴얼의 지침에 따라) | 프린터 설명서, 교체 부품(호환성 여부는 설명서 참조) |
문제 해결 | 일반적인 문제(용지 걸림, 인쇄 오류)는 프린터 설명서의 문제 해결 가이드를 참조하세요. 복잡한 문제에 대한 지원은 EBM 기술 지원팀에 문의하세요. |
필요에 따라 | 프린터 설명서, EBM 기술 지원 연락처 정보(전화번호, 웹사이트) |
장점과 단점 전자빔 용융
기능 | 장점 | 단점 |
---|---|---|
부품 품질 |
고밀도: EBM은 강력한 전자빔이 금속 분말을 완전히 녹여 순 밀도(>99.5%)에 가까운 부품을 만듭니다. 그 결과 단조 금속에 필적하는 뛰어난 기계적 특성을 지닌 튼튼하고 기능적인 부품이 탄생합니다. 복잡한 지오메트리: EBM은 전자 빔을 정밀하게 제어하기 때문에 복잡한 피처와 내부 채널을 제작하는 데 탁월합니다. 다른 적층 제조 공정과 달리 돌출된 피처를 위한 지지 구조가 필요하지 않습니다. |
표면 마감: EBM의 레이어별 용융 공정은 선택적 레이저 용융(SLM)과 같은 기술에 비해 표면 마감이 약간 거칠어집니다. 따라서 매끄러운 외관이 필요한 애플리케이션의 경우 후처리가 필요할 수 있습니다. 정확성: 매우 정밀하지만 EBM의 전자 빔 직경은 본질적으로 SLM에 사용되는 레이저 빔보다 큽니다. 따라서 SLM으로 프린트한 부품에 비해 치수 공차가 약간 덜 정밀할 수 있습니다. |
재료 호환성 | 다양한 금속: EBM은 티타늄 합금, 인코넬, 심지어 일부 희토류 금속을 포함한 다양한 반응성 및 내화성 금속과의 탁월한 호환성을 자랑합니다. 따라서 이러한 고성능 소재가 중요한 애플리케이션에 이상적입니다. | 파우더 처리: EBM에 사용되는 반응성 금속은 산화 및 오염에 매우 취약합니다. 이러한 문제를 방지하기 위해 전체 EBM 프로세스는 진공 환경에서 진행되어야 하므로 복잡성과 비용이 증가합니다. |
속도와 효율성 |
빌드 시간 단축: 전자빔의 높은 에너지 밀도는 특히 대형 부품의 경우 SLM에 비해 더 빠른 용융과 더 빠른 제작 시간을 가능하게 합니다. 자료 재사용: EBM 챔버에서 사용하지 않은 금속 분말은 높은 수준으로 재활용 및 재사용할 수 있어 폐기물 및 재료 비용을 최소화할 수 있습니다. |
레이어별 프로세스: 더 빠른 용융에도 불구하고 EBM의 고유한 레이어별 특성으로 인해 전체 레이어를 한 번에 적층하는 적층 방식에 비해 제작 시간이 더 오래 걸릴 수 있습니다. |
운영 고려 사항 |
진공 환경: EBM 챔버에 고진공 환경이 필요하기 때문에 시스템이 복잡해지고 운영자를 위한 전문 교육이 필요합니다. 안전: EBM 공정에서는 고에너지 전자빔으로 인해 엑스레이가 발생합니다. 작업자를 보호하려면 적절한 안전 프로토콜과 장비가 필수적입니다. |
비용: EBM 기계와 그 운영은 다른 적층 제조 기술에 비해 비용이 많이 드는 경향이 있습니다. 이는 특히 소규모 기업의 경우 진입 장벽이 될 수 있습니다. |
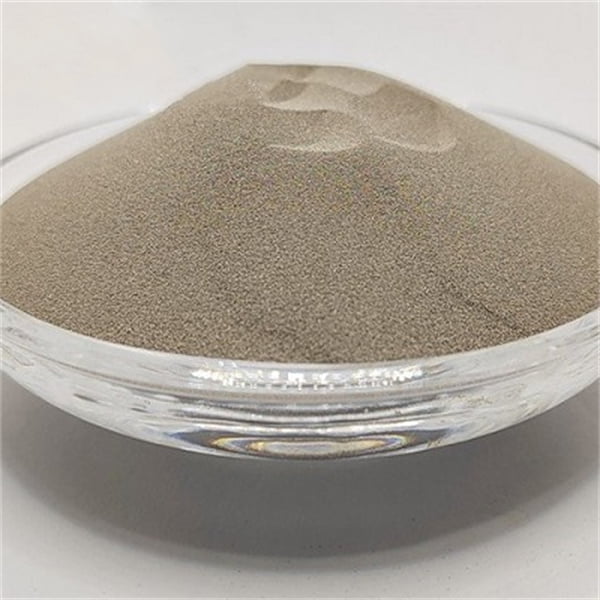
자주 묻는 질문
Q: EBM으로 어떤 재료를 처리할 수 있나요?
A: 현재까지 주로 티타늄, 니켈, 코발트, 스테인리스 스틸 합금이 사용되었습니다. 알루미늄, 공구강, 금, 탄탈륨 등 다양한 소재에 대한 연구를 통해 소재 옵션이 확대되고 있습니다.
Q: EBM과 선택적 레이저 용융(SLM)의 주요 차이점은 무엇인가요?
A: EBM은 전자빔 에너지원을 사용하는 반면 SLM은 레이저를 사용합니다. EBM으로 달성할 수 있는 빔 출력 밀도가 높기 때문에 더 많은 내화성 금속을 가공할 수 있습니다.
Q: 어떤 산업에서 EBM 인쇄를 사용합니까?
A: 항공우주 분야는 터빈 블레이드와 같은 부품을 가장 많이 채택한 분야입니다. 하지만 의료, 자동차, 산업 분야에서도 EBM의 사용자가 증가하고 있습니다.
Q: EBM은 다공성 또는 완전 밀도 부품을 생산하나요?
A: EBM은 최적의 파라미터로 99% 이상의 밀도를 달성할 수 있습니다. 고온 빌드는 레이어 간의 확산 결합을 개선합니다.
Q: EBM으로 어떤 크기의 파트를 제작할 수 있나요?
A: 최대 크기는 빌드 엔벨로프에 의해 제한되며, 일반적으로 약 250 x 250 x 300mm입니다. 더 큰 시스템은 500mm 큐브를 목표로 개발 중입니다.
Q: EBM은 CNC 가공에 비해 얼마나 정확합니까?
A: EBM은 잘 보정된 경우 0.1-0.3mm까지 공차를 달성할 수 있습니다. 그러나 0.05mm 미만의 더 엄격한 공차에 도달하려면 가공이 필요합니다.
질문: EBM의 주요 이점은 무엇인가요?
A: 설계의 자유, 부품 통합, 신속한 프로토타이핑, 고강도 합금, 폐기물 감소, 기존 제조 방식에 비해 짧은 리드 타임.
질문: EBM에는 어떤 안전 예방 조치가 필요하나요?
A: EBM 시스템은 엑스레이 방사선을 방출하므로 빌드 챔버의 적절한 납 차폐가 매우 중요합니다. 숙련된 인력만 작동해야 합니다.