Imagine building complex metal structures layer by layer, with precise control over material properties and minimal waste. This isn’t science fiction; it’s the reality of 직접 에너지 증착 (DED), a revolutionary 3D printing technology that’s transforming the manufacturing landscape.
Directed Energy Deposition, also known by terms like Laser Engineered Net Shaping (LENS) or Direct Metal Deposition (DMD), is an additive manufacturing process that uses a focused energy source, like a laser or electron beam, to melt and deposit metal feedstock material onto a substrate. Think of it like a high-tech welding gun on steroids, building intricate shapes instead of just joining pieces.
This guide dives deep into the world of DED, exploring its functionalities, the diverse metal powders it utilizes, its applications across industries, and the advantages and limitations that define this exciting technology.
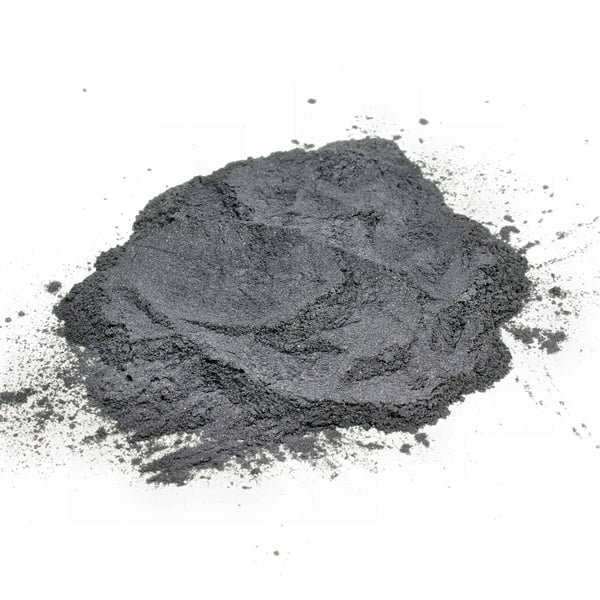
어떻게 직접 에너지 증착 공장
DED operates with a synergy of three key components:
- Energy Source: The heart of DED lies in its concentrated energy source. Lasers and electron beams are the most common choices, offering distinct advantages. Lasers provide high precision and control but can be limited by material reflectivity. Electron beams, on the other hand, delve deeper, offering better penetration for thicker builds, but require a vacuum chamber for operation.
- 공급 원료 재료: The building block of your 3D creation comes in the form of metal powder. DED utilizes a wide range of metal powders, each with unique properties and applications. We’ll delve into the fascinating world of metal powders in a dedicated section later.
- Delivery System: The magic doesn’ t happen without a delivery mechanism. DED employs a nozzle that feeds the metal powder into the molten pool created by the energy source. This precise coordination ensures a seamless layer-by-layer deposition process.
The entire operation is orchestrated by computer-aided design (CAD) software, translating your digital blueprint into precise instructions for the DED system. This allows for the creation of intricate geometries, hollow structures, and features that would be impossible with traditional manufacturing techniques.
A World of Metal Powders: Fueling DED 창작물
The success of DED hinges on the selection of the right metal powder. Just like choosing the perfect ingredients for a recipe, the powder’s properties significantly influence the final product’s characteristics. Here’s a glimpse into ten popular metal powders used in DED:
1. Titanium (Ti): Lightweight, strong, and corrosion-resistant, titanium is a popular choice for aerospace, medical implants, and sporting goods applications. Its biocompatibility makes it ideal for prosthetics and dental implants.
2. Inconel (Nickel-Chromium Alloy): Known for its exceptional high-temperature strength and resistance to oxidation and corrosion, Inconel finds applications in jet engines, heat exchangers, and chemical processing equipment.
3. Stainless Steel (SS): A versatile and cost-effective option, stainless steel offers a good balance of strength, corrosion resistance, and affordability. It’s widely used in automotive parts, medical devices, and general industrial applications.
4. Aluminum (Al): Lightweight and readily available, aluminum is a popular choice for applications where weight reduction is critical, such as aerospace components and automotive parts.
5. Nickel (Ni): Offering good corrosion resistance and electrical conductivity, nickel finds use in electronics, chemical processing equipment, and even some coinage applications.
6. Cobalt-Chrome (CoCr): This biocompatible alloy boasts high strength and wear resistance, making it a preferred choice for orthopedic implants and joint replacements.
7. 구리(Cu): An excellent conductor of heat and electricity, copper finds applications in heat sinks, electrical components, and even for creating intricate microfluidic channels.
8. 텅스텐(W): Renowned for its incredibly high melting point and exceptional wear resistance, tungsten is used for applications like welding electrodes, armor-piercing projectiles, and high-temperature furnace components.
9. Molybdenum (Mo): Similar to tungsten, molybdenum offers high-temperature strength and finds applications in aerospace components, nuclear reactors, and filaments for lighting applications.
10. Hastelloy: This family of nickel-based superalloys boasts exceptional resistance to a wide range of corrosive environments, making them ideal for applications in the chemical processing, oil and gas, and power generation industries.
This list just scratches the surface of the vast array of metal powders available for DED. The choice of powder depends on the desired properties of the final product, such as strength, weight, corrosion resistance, and thermal conductivity.
Beyond the Basics: A Breakdown of Metal Powders Properties
속성 | 설명 | Importance in DED |
---|---|---|
입자 크기 및 분포: | Refers to the size and variation in size of the metal powder particles. | Influences flowability, packing density, and surface finish of the final product. Consistent particle size ensures smooth deposition and minimizes porosity. |
구형성: | The degree to which a particle resembles a perfect sphere. | Spherical particles flow more easily, pack more densely, and result in better surface finish compared to irregularly shaped particles. |
흐름성: | 파우더가 흐르는 용이성. | Critical for consistent material feed into the DED system. Poor flowability can lead to feeding issues and inconsistencies in the final product. |
겉보기 밀도: | 파우더의 벌크 밀도입니다. | влияет (vliyaniyet) on (on) the amount of material required to build a part and can impact production costs. |
녹는점: | The temperature at which the powder transitions from solid to liquid. | Needs to be compatible with the chosen energy source to ensure proper melting and deposition. |
화학 성분: | The elemental makeup of the powder. | Dictates the final properties of the printed part, such as strength, corrosion resistance, and electrical conductivity. |
올바른 파우더 선택하기: 균형 잡기
Selecting the optimal metal powder for your DED project requires careful consideration of several factors. Here’s a breakdown to help you navigate this decision:
- 신청 요건: The intended use of the final product is paramount. For instance, a component for a jet engine will necessitate a high-temperature resistant powder like Inconel, whereas a medical implant might require a biocompatible option like titanium or cobalt-chrome.
- 원하는 속성: Identify the crucial characteristics you need in the finished part. Is strength the top priority? Perhaps corrosion resistance or lightweight construction is essential. Understanding these needs will guide your powder selection.
- Compatibility with DED System: Ensure the chosen powder aligns with the capabilities of your DED machine. Consider factors like laser power or the availability of a vacuum chamber for electron beam DED.
- 비용 및 가용성: Metal powders can vary significantly in price. Balance your budgetary constraints with the desired properties and explore the availability of the powder to avoid production delays.
Additional Considerations for 직접 에너지 증착
While metal powders reign supreme in DED, the future holds promise for incorporating other materials. Researchers are exploring the potential of using:
- 합성물: Blending metal powders with ceramic or polymer particles to create materials with unique combinations of properties, like improved wear resistance or electrical conductivity.
- 기능적으로 등급이 매겨진 재료(FGM): Gradually transitioning between different materials within a single build to achieve specific functionalities across different regions of the part. Imagine a tool with a wear-resistant tip transitioning to a lighter weight handle – all printed in one go with DED.
These advancements open exciting possibilities for DED, pushing the boundaries of design and functionality in future applications.
응용 직접 에너지 증착
DED’s versatility shines through its diverse range of applications across numerous industries. Here are some compelling examples:
- 항공우주: DED excels in creating lightweight, high-strength components for aircraft, such as wing ribs, landing gear parts, and even rocket engine components. The ability to produce complex geometries with minimal waste makes DED a game-changer in this weight-critical industry.
- 의료용 임플란트: DED’s ability to create biocompatible parts with intricate designs makes it ideal for custom-made prosthetics, dental implants, and even cranial implants. This technology personalizes medical care, improving patient outcomes and quality of life.
- 자동차: The automotive industry is embracing DED for prototyping and low-volume production of high-performance parts. DED allows for the creation of lightweight components and complex internal structures that traditional manufacturing might struggle with.
- Tooling and Repair: DED offers a rapid and cost-effective way to create and repair jigs, fixtures, and cutting tools. Imagine repairing a damaged mold or creating a custom tool on-demand – DED makes it possible.
- 석유 및 가스: DED finds applications in creating corrosion-resistant components for downhole tools and other equipment used in the harsh oil and gas environments.
- 소비재: From customized eyewear frames to design-driven bicycle components, DED is making its way into the consumer goods market, enabling the creation of unique and innovative products.
These are just a few examples, and as DED technology matures, we can expect even more groundbreaking applications to emerge across various industries.
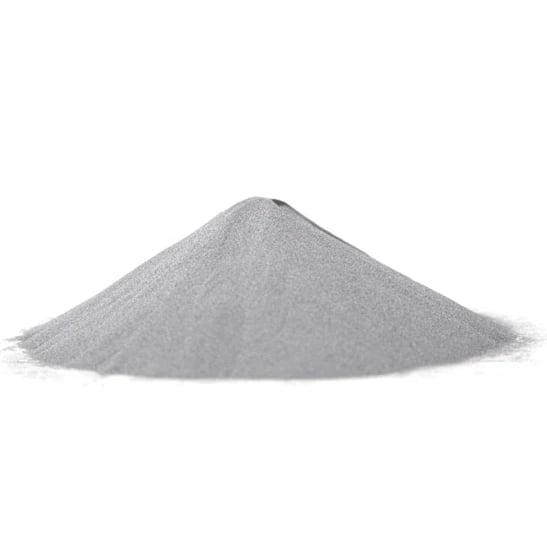
의 장점과 한계 직접 에너지 증착
DED boasts a compelling set of advantages that make it a disruptive force in manufacturing. But like any technology, it comes with its own limitations. Let’s delve into both sides of the coin.
Advantages of Directed Energy Deposition:
- 자유로운 디자인: Unleash your creativity! DED allows for the creation of intricate geometries, including thin walls, lattices, and undercuts that would be impossible or highly challenging with traditional techniques. This opens doors for lightweight and highly functional designs.
- 재료 효율성: DED is a near-net-shape manufacturing process, meaning minimal material goes to waste. The unused powder can often be recycled, minimizing waste and production costs.
- 신속한 프로토타이핑: DED’s ability to quickly create functional prototypes accelerates the product development cycle, allowing for faster design iterations and time to market.
- 사용자 지정: DED shines in creating custom-made parts, perfectly tailored to specific needs. This is particularly valuable in industries like medical implants and aerospace.
- 파트 통합: DED can combine multiple components into a single piece, simplifying designs, reducing assembly time, and potentially improving part performance.
- 다용도성: A wide range of metal powders, and potentially other materials in the future, broadens the application landscape of DED.
의 제한 사항 직접 에너지 증착:
- 빌드 속도: Compared to traditional techniques like casting or injection molding, DED can be slower, especially for larger parts. This is an ongoing area of development, with research focused on faster deposition rates.
- 표면 거칠기: The layer-by-layer nature of DED can result in a stair-step effect on the surface finish. Post-processing techniques like machining or polishing might be required to achieve a smoother finish.
- 머티리얼 속성: While DED parts can achieve excellent mechanical properties, they might not always perfectly match those of wrought or forged metals due to the inherent nature of the additive manufacturing process. Further research and development are ongoing to optimize DED processes for various materials.
- 비용: DED systems can be expensive, and the cost of metal powders can vary significantly. This might limit its adoption for high-volume production of low-cost parts.
- 잔여 스트레스: The rapid heating and cooling cycles during DED can introduce residual stress into the part. Proper design and post-processing techniques can help mitigate this issue.
자주 묻는 질문
Here are some of the most common questions people have about DED:
Q: What are the advantages of DED over other 3D printing technologies like FDM (Fused Deposition Modeling)?
A: DED offers several advantages over FDM. Firstly, DED utilizes metal powders, enabling the creation of functional metal parts. FDM, on the other hand, is typically limited to plastics and other polymers. Secondly, DED parts generally boast superior mechanical properties compared to FDM parts. Finally, DED allows for a wider design freedom with the ability to create complex geometries.
Q: Can DED be used to repair metal parts?
A: Absolutely! DED’s ability to precisely deposit material makes it ideal for repairing damaged metal components. This can be a cost-effective and time-saving solution compared to traditional replacement methods.
Q: What is the future of Directed Energy Deposition?
A: The future of DED is bright! We can expect advancements in several areas:
- Faster Build Speeds: Researchers are continuously developing methods to increase deposition rates, making DED more competitive for larger-scale production.
- Multi-Material DED: The ability to seamlessly combine different metal powders or even metal and non-metal materials within a single build opens exciting possibilities for creating parts with tailored properties in different regions.
- 표준화: As DED technology matures, standardization of processes and materials will play a crucial role in ensuring quality and repeatability.
- 비용 절감: With advancements in technology and increased adoption, the cost of DED systems and metal powders is expected to come down, making DED more accessible to a wider range of manufacturers.
DED holds immense potential to revolutionize various industries. Its ability to create complex, functional metal parts with minimal waste and high design freedom makes it a technology to watch. As DED continues to evolve, we can expect even more groundbreaking applications to emerge, shaping the future of manufacturing.