디지털 아티스트의 정밀함으로 복잡한 금속 물체를 한 겹 한 겹 조각하여 처음부터 다시 만든다고 상상해 보세요. 이것이 바로 3D 프린팅 금속 분말이 혁신적인 기술의 핵심에는 중요한 요소가 있습니다: 금속 분말. 그렇다면 고체 금속을 3D 프린팅에 필요한 미세하고 유동적인 분말로 어떻게 변환할 수 있을까요? 입력 물 분무이 가이드의 중심이 되는 강력하고 다재다능한 기술입니다.
마법을 공개합니다: 물 분무란 무엇인가요?
물 분무는 용융 금속을 작은 물방울로 이루어진 미세한 안개로 바꾸는 기술이라고 생각하면 됩니다. 단순해 보이는 이 과정에는 엄청난 힘이 숨어 있습니다. 작동 원리는 다음과 같습니다:
- 금속을 녹입니다: 여정은 선택한 금속을 용광로에서 용융 상태로 가열하는 것으로 시작됩니다. 용융된 금속으로 빛나는 불타는 도가니가 변신할 준비가 되었다고 상상해 보세요.
- 고압 H2O: 다음으로 고압 워터 제트가 용융 금속 흐름에 분사됩니다. 소방관의 스테로이드 호스와 유사한 이 강력한 물 분사는 액체 금속을 작은 물방울의 미세한 스프레이로 분해합니다.
- 빠른 고형화: 금속 방울이 흩어지면서 공중에서 빠르게 냉각되고 응고되어 개별 금속 분말 입자를 형성합니다. 작은 금속 빗방울이 땅에 떨어지기도 전에 굳어지는 모습을 상상해 보세요.
- 수집 및 처리: 새로 형성된 금속 분말을 수집, 건조, 체질하여 원하는 입자 크기와 분포를 얻습니다. 이를 통해 3D 프린팅 애플리케이션의 일관성과 최적의 성능을 보장합니다.
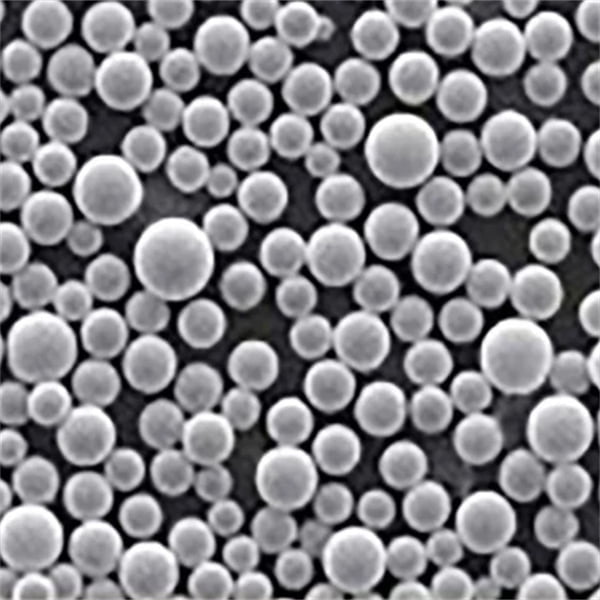
3D 프린팅 금속 분말: 왜 이 방법을 선택해야 하나요?
기능 | 혜택 | 설명 |
---|---|---|
자유로운 디자인 | Highly complex geometries | Unlike traditional methods like machining or casting that rely on subtractive or formative techniques, 3D printing with metal powders builds parts layer-by-layer directly from a digital model. This enables the creation of intricate internal features, channels, and lattice structures that would be impossible or highly impractical with other methods. |
소재의 다양성 | 광범위한 금속 | Metal powders are available in a vast array of options, from common metals like titanium and aluminum to more exotic materials like Inconel and precious metals like gold. This allows engineers to choose the perfect material for the specific application, considering factors like strength, weight, corrosion resistance, and biocompatibility. |
신속한 프로토타이핑 | Faster design iteration | The digital nature of 3D printing allows for quick and easy design changes. Modifications can be made to the CAD model and a new prototype can be printed within a short timeframe. This significantly reduces development time and cost compared to traditional prototyping methods. |
경량화 | Design for efficiency | The ability to create complex internal structures with 3D printing metal powders allows for parts to be lightweight while maintaining their strength. This is crucial in applications like aerospace and automotive where weight reduction translates to improved fuel efficiency and performance. |
온디맨드 제조 | Reduced inventory needs | 3D printing with metal powders enables parts to be produced as needed, eliminating the requirement for large production runs and storage of finished goods. This is particularly beneficial for low-volume production or spare parts that may not be readily available through traditional channels. |
Minimal Material Waste | 지속 가능한 생산 | Metal 3D printing only uses the material required to build the part, unlike traditional methods that generate significant scrap material. This reduces waste and lowers the environmental impact of the manufacturing process. |
사용자 지정 | Personalized products | The ability to create complex geometries with 3D printing metal powders allows for the production of highly customized parts. This is beneficial for applications like medical implants, prosthetics, and dental crowns that require a perfect fit for each individual. |
Consolidation of Parts | Reduced assembly complexity | The design freedom offered by 3D printing metal powders allows for the creation of complex parts that integrate the functionality of multiple components. This reduces assembly complexity, lowers production costs, and improves the overall performance of the product. |
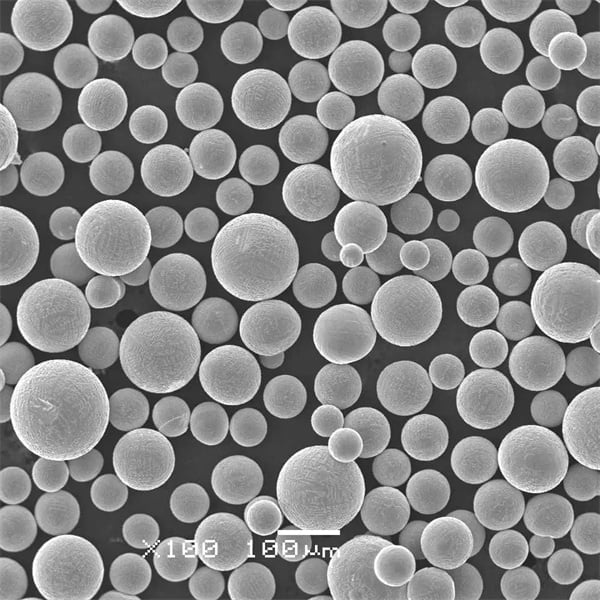
3D 프린팅의 물 분무 응용 분야: 금속에 생명력 불어넣기
프로세스 | 설명 | 장점 | 단점 |
---|---|---|---|
물 분무 | Molten metal is transformed into a fine powder through a multi-step process. First, the metal is melted in a furnace. Then, a high-pressure nozzle forces the liquid metal into a thin stream. This stream is broken into tiny droplets by a high-velocity water jet. Finally, the rapidly cooled droplets solidify into individual powder particles, which are collected, dried, and sieved to achieve a specific size and distribution. | – Cost-effective: Water atomization offers a relatively low-cost method for producing large quantities of metal powder compared to other techniques. – Wide material compatibility: This method can handle a broad spectrum of metals, from common varieties like steel and aluminum to more specialized options. |
– Particle shape: Water-atomized powders tend to be less spherical than those produced by other methods. This can affect the flowability of the powder and the packing density within the 3D printing bed, potentially impacting the surface quality of the final printed part. |
선택적 레이저 용융(SLM) | A 3D printing technique that utilizes a high-powered laser to selectively melt and fuse metal powder particles layer by layer. The laser beam follows a digital design, building up the desired 3D object. | – High precision and accuracy: SLM allows for the creation of complex geometries with tight tolerances, making it ideal for intricate metal parts. – Design freedom: Unlike traditional manufacturing methods, SLM offers significant design freedom, enabling the production of parts with internal channels, lattices, and other unique features. |
– Limited build volume: Current SLM machines typically have a restricted build volume, limiting the size of printable objects. – Surface roughness: The layer-by-layer nature of SLM can result in a slightly rough surface finish on the printed parts, which may require additional post-processing. |
전자빔 용융(EBM) | Similar to SLM, EBM employs a high-powered beam, but in this case, an electron beam operates in a vacuum environment. The electron beam melts the metal powder particles, fusing them together to form the desired 3D object. | – Superior mechanical properties: EBM produces parts with excellent mechanical properties, including high strength and good fatigue resistance. This is due to the vacuum environment, which minimizes oxidation and enhances material properties. – Broader material compatibility: Compared to SLM, EBM offers compatibility with a wider range of metals, including reactive materials like titanium. |
– Higher cost: EBM systems are generally more expensive than SLM machines, impacting the overall cost of production. – Vacuum requirement: The need for a vacuum environment adds complexity to the EBM process and can limit its accessibility in certain settings. |
바인더 제팅(BJ) | A 3D printing method that utilizes a liquid binding agent to selectively inkjet metal powder particles onto a printing platform. The layers are then cured to create a solid structure. | – High build volume: Binder jetting offers a larger build volume compared to SLM and EBM, enabling the production of bigger metal parts. – Potential for full-color printing: In development are binder jetting techniques that incorporate colored binders, opening doors for the creation of functional and visually appealing metal parts. |
– Lower part strength: Parts produced through binder jetting typically exhibit lower strength compared to those made with SLM or EBM. This may necessitate additional post-processing steps, such as infiltration, to achieve the desired mechanical properties. – Limited material options: Currently, binder jetting has a more limited range of compatible metal materials compared to other 3D printing methods. |
Choosing the Right Water-Atomized Metal Powder
팩터 | 설명 | Impact on Additive Manufacturing Process & Final Part |
---|---|---|
머티리얼 속성 | The specific metal or alloy chosen will dictate the final properties of the 3D printed part. | • 강도 및 내구성: Consider applications requiring high strength-to-weight ratios like aerospace components. Nickel alloys or titanium powders excel here. • 내식성: Parts exposed to harsh environments might benefit from stainless steel or copper alloys. • Thermal Conductivity & Electrical Conductivity: Heat sinks or electrical conductors might utilize aluminum or copper powders for optimal performance. |
입자 크기 및 분포 | The size and variation in size of the powder particles significantly affect printability and final part characteristics. | • 흐름성: Uniform, spherical particles flow more easily, leading to consistent layer formation during printing. • 포장 밀도: The ideal powder packing density allows for maximum material utilization while enabling proper fusion between layers. • 표면 마감: Finer powders generally result in smoother surface finishes on the final part. • 기계적 속성: Particle size and distribution can influence the final part’s strength, porosity, and ductility. |
입자 형태학 | The shape of the powder particles influences their packing behavior and flowability. | • 구형성: Highly spherical particles offer superior flowability and packing density, leading to improved printability. • Satellites & Satellited Particles: These are smaller particles attached to larger ones. Excessive satellites can hinder flowability and lead to inconsistencies in the printed part. • Hollow Particles: While offering weight reduction benefits, hollow particles can create internal voids in the final part, impacting its mechanical strength. |
Chemical Composition & Powder Purity | The presence of impurities or deviations from the desired chemical makeup can affect the printing process and final part quality. | • 산소 함량: Excessive oxygen can lead to higher porosity and reduced mechanical properties. • 수분 함량: Moisture can cause spattering during the printing process and lead to surface defects. • 추적 요소: The presence of unintended elements can influence the material’s properties and printability. Reputable suppliers provide detailed chemical analysis reports to ensure adherence to material specifications. |
분말 유동성 | The ease with which the powder flows is crucial for consistent layer formation in additive manufacturing processes. | Poor flowability can lead to: • Inconsistent layer thickness • Segregation of particles within the powder bed • Difficulties with material spreading mechanisms These issues can all negatively impact the quality and dimensional accuracy of the final part. |
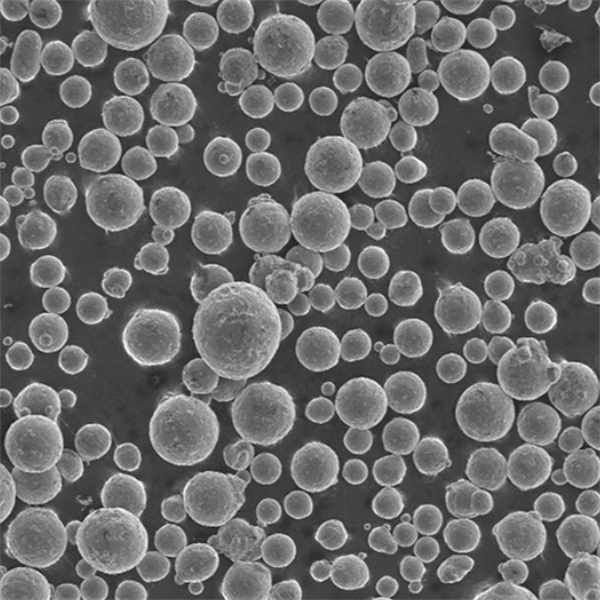
Advanced Considerations for Water Atomization
팩터 | 설명 | Impact on Process | 완화 전략 |
---|---|---|---|
Multi-Component Feedstock | When atomizing alloys or slurries containing multiple components, factors like particle size distribution and composition uniformity become critical. | Segregation of components can occur during atomization, leading to variations in final product properties. | – Controlled Mixing: Utilizing high-shear mixers or inline homogenizers can ensure uniform distribution of components within the feedstock. – Co-Atomization: Simultaneous atomization of individual elements can be employed to achieve precise control over final composition. – Monitoring and Feedback Systems: Real-time monitoring of particle size and composition allows for adjustments to atomization parameters for consistent product quality. |
입자 형태학 | The shape and surface characteristics of the atomized particles significantly influence downstream processes like powder handling, sintering, and final product performance. | Irregular particle shapes can lead to challenges in packing density, flowability, and sintering behavior. | – Atomization Pressure and Nozzle Design: Optimizing these parameters can influence the degree of droplet break-up and solidification, leading to more spherical particles. – Surfactant Selection: Specific surfactants can be introduced into the water stream to modify surface tension and promote more uniform particle morphology. – 빠른 고형화: Techniques like high-pressure atomization or rapid quenching can minimize particle growth and promote more spherical shapes. |
환경 영향 | Water atomization processes can generate wastewater containing metal particles and require significant water consumption. | Untreated wastewater disposal poses environmental hazards. High water usage can strain resources. | – Water Recycling Systems: Closed-loop systems can be implemented to capture and treat the atomization water, minimizing waste and water consumption. – Flocculation and Settling: These techniques can be used to separate metal particles from the wastewater before treatment and disposal. – Advanced Filtration Systems: Membrane filtration or ion exchange processes can be employed for high-efficiency removal of contaminants from wastewater. |
Process Automation and Control | Integration of automation and real-time process control can significantly improve consistency and efficiency. | Manual operation can lead to human error and inconsistencies in product quality. | – Automated Control Systems: Implementing feedback loops and automated adjustments based on sensor data ensures consistent product quality. – Advanced Monitoring Systems: Real-time monitoring of critical parameters like flow rates, pressures, and particle characteristics allows for proactive adjustments and optimization. – Machine Learning Integration: Machine learning algorithms can analyze historical data and sensor readings to predict potential issues and optimize process parameters for improved efficiency and yield. |
안전 고려 사항 | Water atomization processes involve high pressures, moving parts, and potential exposure to metal particulates. | Improper safety procedures can lead to accidents and injuries. | – Proper Training and Personal Protective Equipment (PPE): Thorough training for operators on safe handling procedures and the use of appropriate PPE is crucial. – 정기 유지 관리 및 검사: Implementing preventative maintenance schedules and safety inspections minimizes equipment failure and potential hazards. – Enclosure Design and Ventilation Systems: Enclosing high-pressure areas and utilizing proper ventilation systems mitigate exposure to airborne metal particles. |
자주 묻는 질문
질문 | 답변 |
---|---|
3D 프린팅용 물 분무 금속 분말의 일반적인 입자 크기는 얼마입니까? | 입자 크기 범위는 일반적으로 다음과 같습니다. 10~150 마이크로미터(µm) 사이특정 범위는 선택한 금속과 원하는 용도에 따라 달라집니다. |
물로 원자화된 금속 분말을 재활용할 수 있나요? | 예, 물로 분무된 금속 분말은 다음과 같습니다. 재활용 다음과 같은 다양한 기술을 통해 재용융 및 재원자화. 이는 다음을 촉진합니다. 지속 가능성 및 폐기물 감소. |
물 분무는 다른 금속 분말 생산 방법과 어떻게 다릅니까? | 물 분무는 다음과 같은 측면에서 이점을 제공합니다. 비용 효율성 및 생산 속도와 같은 다른 방법 가스 분무 를 반환할 수 있습니다. 더 많은 구형 입자 에 적합하며 반응성 금속. 선택은 궁극적으로 특정 애플리케이션과 원하는 속성에 따라 달라집니다. |
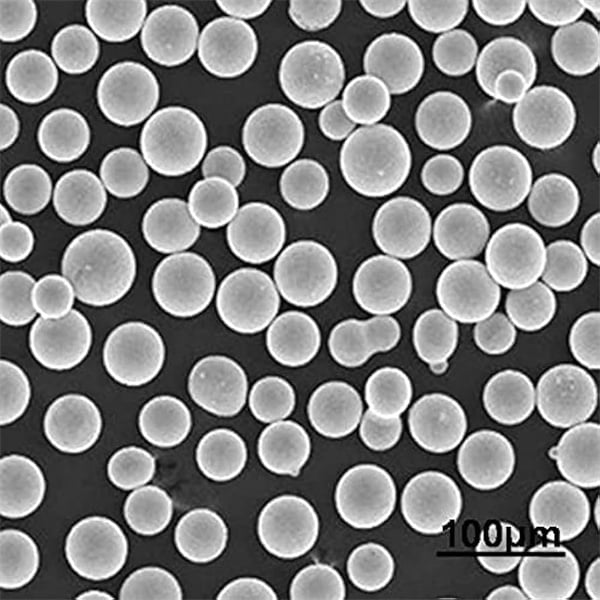
결론 결론: 물 분무의 잠재력 수용하기
3D 프린팅의 세계가 계속 발전함에 따라 물 분무는 여전히 초석 기술로 남아 있으며, 다음과 같은 이점을 제공합니다. 안정적이고 비용 효율적인 는 다양한 용도의 금속 분말을 생산하는 것을 의미합니다. 에서 복잡한 항공우주 부품 에 복잡한 의료용 임플란트물 분무 분말을 사용하면 다양하고 기능적인 3D 프린팅 부품을 제작할 수 있습니다.
앞으로 물 분무의 미래는 잠재력이 무궁무진합니다. 지속적인 기술 발전이 약속합니다:
- 향상된 파티클 모양: 통해 분무 기술의 개선 및 혁신적인 소재에 대한 탐구에서 구형성 의 물 분무 분말을 더욱 개선할 수 있습니다. 품질 일치 가스 분무와 같은 더 비싼 방법으로 달성할 수 있습니다.
- 확장된 소재 호환성: 연구자들은 물 분무의 잠재력을 적극적으로 탐구하고 있습니다. 더 광범위한 금속다음을 포함합니다. 반응성이 높은 재료 기존 방식으로는 해결하기 어려운 문제를 해결합니다. 이를 통해 다음과 같은 까다로운 산업 분야에서 3D 프린팅 애플리케이션의 새로운 길을 열 수 있습니다. 항공우주 및 의학.
- 지속 가능한 발전: 다음 사항에 중점을 둡니다. 환경적 책임 의 개발을 주도하고 있습니다. 친환경 물 분무 공정. 여기에는 다음이 포함될 수 있습니다. 폐쇄형 루프 시스템 물 사용량과 폐기물 발생을 최소화하여 더 많은 지속 가능한 미래 3D 프린팅 금속 분말 생산에 사용됩니다.
물 분무화의 잠재력을 수용하고 그 한계를 지속적으로 확장함으로써 3D 프린팅 금속이 훨씬 더 많이 활용되는 미래를 열 수 있습니다. 강력하고 다재다능한 기술혁신적이고 변화하는 방식으로 우리 주변의 세상을 만들어가고 있습니다.