단조나 가공이 아닌 한 겹 한 겹 세심하게 만들어진 복잡한 금속 물체를 손에 쥐고 있다고 상상해 보세요. 이것이 바로 3D 프린팅 금속 분말, a revolutionary technology transforming manufacturing across industries. But how exactly does this process work, and how can you leverage it for your projects? Buckle up, because we’re diving deep into the world of metal alchemy, one grain of powder at a time!
Steps for Using 3D 프린팅 금속 분말
While 3D printing metal powder might sound like science fiction, the basic steps are surprisingly logical. Here’s a breakdown of the journey from your imagination to a tangible metal masterpiece:
- 디지털 디자인: The first step is crafting a digital blueprint of your creation. This can be done using 3D modeling software, ensuring intricate details and precise dimensions. Think of it as the architect’s meticulously crafted plan before building a magnificent structure.
- 파우더 선택: With your design locked in, it’s time to choose the metal powder best suited for your project. Common choices include stainless steel, titanium, aluminum, and even exotic alloys like Inconel. Each metal powder boasts unique properties like strength, weight, and heat resistance. Selecting the right powder is akin to picking the perfect ingredients for a delicious recipe – it dictates the final product’s functionality and aesthetics.
- 인쇄 프로세스: Here’s where the real magic happens! Your design is sliced into ultrathin layers, and a specialized 3D printer meticulously lays down a bed of metal powder. A high-powered laser or electron beam then selectively melts the powder particles, fusing them together layer by layer according to your digital blueprint. Imagine a skilled artist meticulously adding tiny brushstrokes to create a breathtaking masterpiece – that’s the essence of this stage.
- 후처리: Once the printing is complete, the part needs some additional TLC. Support structures used during printing are removed, and the part might undergo heat treatment to enhance its mechanical properties. This post-processing phase is like the final touches an artist gives to their creation, ensuring a flawless finish.
- Voila! Your Metal Marvel: Congratulations! You’ve successfully transformed a digital concept into a tangible metal object. 3D printed metal parts can be incredibly complex, lightweight, and boast superior strength compared to traditional manufacturing methods. It’s like holding the future in your hands!
하지만 잠깐만요, 더 있습니다! While these core steps provide a roadmap, the nuances of 3D printing metal powder can vary depending on the specific technology used. Let’s delve into the two most common methods:
- 선택적 레이저 용융(SLM): This technique utilizes a high-powered laser to melt metal powder particles. SLM offers exceptional detail and accuracy, making it ideal for intricate parts with complex geometries. Think of it as the most meticulous artist in the metal printing world.
- 전자 빔 용융(EBM): EBM harnesses a powerful electron beam to melt metal powder in a vacuum chamber. This method is particularly well-suited for creating parts from reactive metals like titanium, which can be susceptible to oxidation in traditional printing environments. Imagine working in a specialized, controlled environment to ensure the best possible outcome for your creation – that’s the essence of EBM.
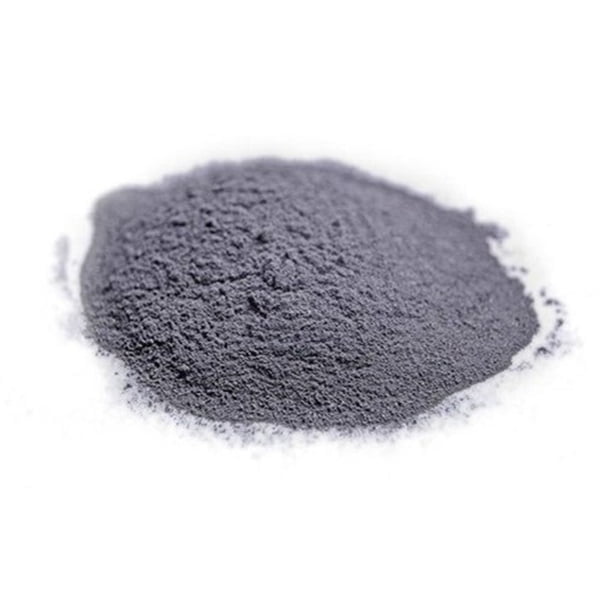
The Application of 3D Printing Metal Powder
애플리케이션 3D 프린팅 금속 분말 are truly boundless, stretching across various industries and igniting a wave of innovation. Here are just a few captivating examples:
- 항공우주: The lightweight and high-strength properties of 3D printed metal components are perfect for the aerospace industry. Complex rocket parts, intricate heat exchangers, and even customized fuel injectors are being produced using this technology, leading to lighter, more fuel-efficient spacecraft. Imagine spaceships shedding unnecessary weight, soaring through the cosmos with newfound agility – that’s the impact of 3D printed metal powder in aerospace.
- 의료: The medical field is witnessing a revolution with 3D printed metal implants. Customized prosthetics, intricate surgical instruments, and even biocompatible metal structures for bone repair are now possible. This technology offers a new level of personalization and precision in medical care, improving patient outcomes and offering hope for those in need.
- 자동차: The automotive industry is embracing 3D printed metal components to create lighter, more fuel-efficient vehicles. Customized engine parts, intricate cooling systems, and even lightweight brackets are being produced using this method. Imagine cars shedding pounds and gaining miles per gallon – that’s the transformative power of 3D printed metal powder in the automotive world.
The Advantages and Disadvantages of 3D Printing Metal Powder
3D printing metal powder boasts a treasure trove of advantages, but like any technology, it has limitations to consider. Here’s a balanced perspective to help you decide if this method aligns with your project’s needs:
장점:
- 자유로운 디자인: Unleash your creativity! Unlike traditional manufacturing techniques limited by tools and subtractive methods, 3D printing allows for complex geometries, intricate internal channels, and even lattice structures for weight reduction. Imagine sculpting your design with unparalleled freedom – that’s the liberating aspect of 3D printed metal powder.
- 경량화: Metal parts produced via 3D printing can be significantly lighter compared to traditionally machined counterparts. This translates to numerous benefits depending on the application. In aerospace, lighter components translate to increased fuel efficiency and longer flight ranges. In the automotive industry, it equates to improved gas mileage and reduced emissions. Think of shedding unnecessary weight and achieving superior performance – that’s the power of lightweighting with 3D printed metal powder.
- 신속한 프로토타이핑: Gone are the days of lengthy and expensive prototyping processes. 3D printing allows for quick and iterative creation of physical prototypes, enabling designers and engineers to test form and function efficiently. Imagine rapidly bringing your ideas to life and refining them with ease – that’s the agility advantage of 3D printed metal powder.
- 사용자 지정: Mass production doesn’t have to mean uniformity. 3D printing excels at creating customized metal parts, perfect for applications requiring a perfect fit or unique functionality. Imagine crafting bespoke components tailored to specific needs – that’s the power of customization offered by 3D printed metal powder.
- 낭비 감소: Traditional manufacturing often generates significant scrap metal. 3D printing, on the other hand, uses a more additive approach, minimizing material waste. This translates to both cost savings and environmental benefits. Imagine using metal powder efficiently and minimizing environmental impact – that’s the sustainable advantage of 3D printed metal powder.
단점:
- 비용: While costs are steadily decreasing, 3D printing metal powder can still be a relatively expensive process compared to traditional methods for high-volume production. The specialized equipment, metal powders, and post-processing steps contribute to the overall cost. Imagine a high-end, specialized service compared to a more mass-produced approach – that’s the cost consideration with 3D printed metal powder.
- 빌드 크기 제한: Current 3D metal printers have limitations on the size of parts they can produce. This might not be suitable for large-scale industrial applications requiring massive components. Imagine working with a smaller canvas compared to traditional methods with potentially limitless build sizes – that’s the size constraint to consider with 3D printed metal powder.
- 표면 마감: While 3D printed metal parts can achieve good surface finishes, they might not always match the smoothness achievable with traditional machining techniques like polishing. The layer-by-layer nature of the printing process can sometimes leave a slightly textured surface. Imagine a handcrafted, unique finish compared to a perfectly polished, mass-produced look – that’s the surface finish consideration with 3D printed metal powder.
- 자료 가용성: The variety of metal powders readily available for 3D printing is still expanding compared to the vast selection of metals used in traditional manufacturing. This might limit options for specific projects requiring unique material properties. Imagine having a curated selection of ingredients compared to a vast supermarket aisle – that’s the material availability consideration with 3D 프린팅 금속 분말.
Finding the Right Fit
With a clearer understanding of the advantages and limitations, you can make an informed decision about whether 3D printing metal powder is the right choice for your project. Here are some scenarios where this technology shines:
- 프로토타이핑: When rapid creation and design iteration are crucial, 3D printed metal prototypes offer unmatched speed and flexibility.
- Low-volume Production: For projects requiring small batches of specialized metal parts, 3D printing can be more cost-effective and agile than traditional manufacturing methods.
- 복잡한 지오메트리: If your design boasts intricate features or internal channels, 3D printing allows for unparalleled design freedom compared to subtractive manufacturing techniques.
- 경량화: When weight reduction is paramount, 3D printed metal components can offer significant advantages in industries like aerospace and automotive.
- 사용자 지정: For applications requiring bespoke metal parts with a perfect fit or unique functionality, 3D printing offers unmatched customization capabilities.
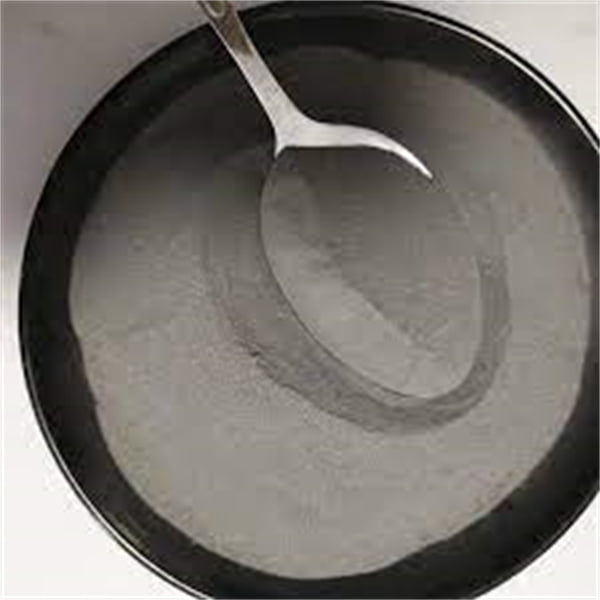
자주 묻는 질문
Q: What are the different types of metal powders used in 3D printing?
A: A wide variety of metal powders are used, including common metals like stainless steel, titanium and aluminum, as well as specialty alloys like Inconel and cobalt chrome. The choice of metal powder depends on the desired properties of the final part, such as strength, weight, heat resistance, and corrosion resistance.
Q: Is 3D printed metal powder safe to handle?
A: Metal powders can be fine and pose inhalation risks. Proper safety precautions are crucial, including using a ventilated workspace, wearing personal protective equipment like masks and gloves, and following the specific safety guidelines for the particular metal powder being used.
Q: How strong are 3D printed metal parts?
A: The strength of 3D printed metal parts can vary depending on the metal powder used, the printing process, and post-processing techniques. However, 3D printed metal parts can achieve very high strength levels comparable to traditionally manufactured counterparts.
Q: What are the surface finish options for 3D printed metal parts?
A: While the layer-by-layer nature of 3D printing can result in a slightly textured surface, various post-processing techniques can be used to achieve smoother finishes. These techniques include sandblasting, polishing, and machining.
Q: What is the future of 3D printing metal powder?
A: The future of 3D printing metal powder is incredibly exciting. Advancements are expected in several areas, including:
- 비용 절감: As technology matures and adoption increases, the cost of 3D printing metal powder is expected to decrease, making it more accessible for a wider range of applications.
- 빌드 크기 증가: Developments in printer technology are expected to allow for the creation of larger metal parts, opening doors for new industrial applications.
- 확장된 머티리얼 선택: The variety of metal powders available for 3D printing is continually expanding, offering more options for engineers and designers.
- 다중 재료 인쇄: Emerging technologies are paving the way for 3D printing metal parts with integrated features from different materials, opening doors for even more complex and functional creations.